Guzman Polymers & Prosilas Press Release Energia Plus ICP Magazine Newsby Are Your R -...
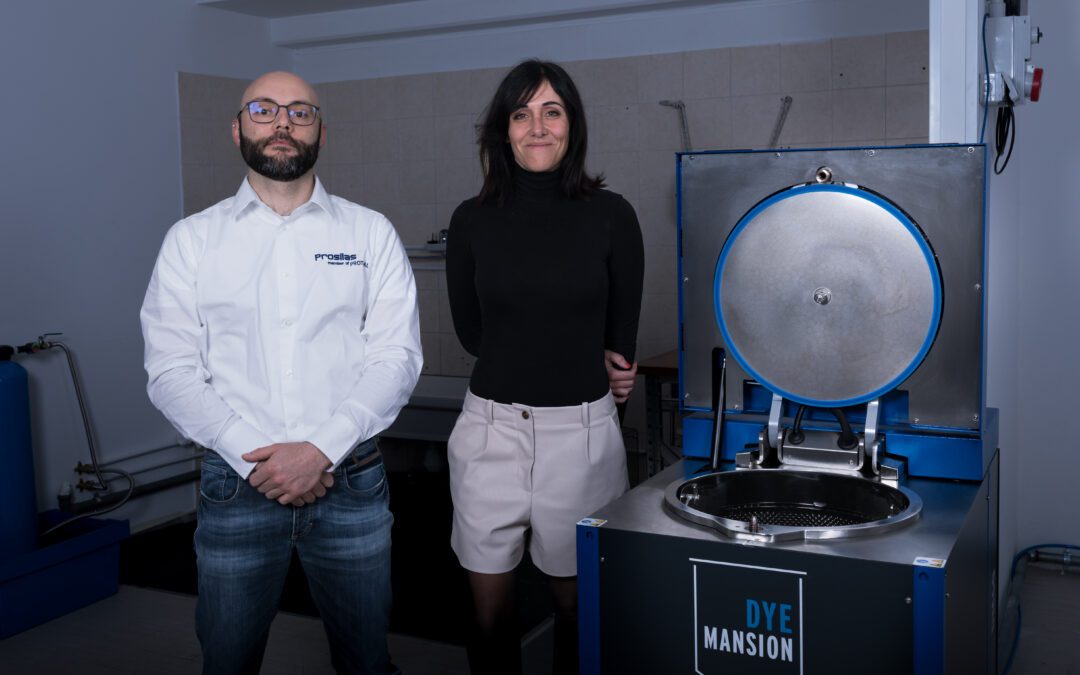
Prosilas acquires the DM 60 DyeMansion automated coloring system.
The New DM60 for Prosilas
Industrial coloring of 3D printed parts.
3D printing is making great strides in the industrial sector, thanks in part to new automated finishing and coloring systems for prototypes and finished components.
And at Prosilas, we’re not just standing by!
In fact, we’ve expanded our machinery lineup with the DM60 DyeMansion automated coloring system, thereby closing the post-production cycle already present in our company.
.
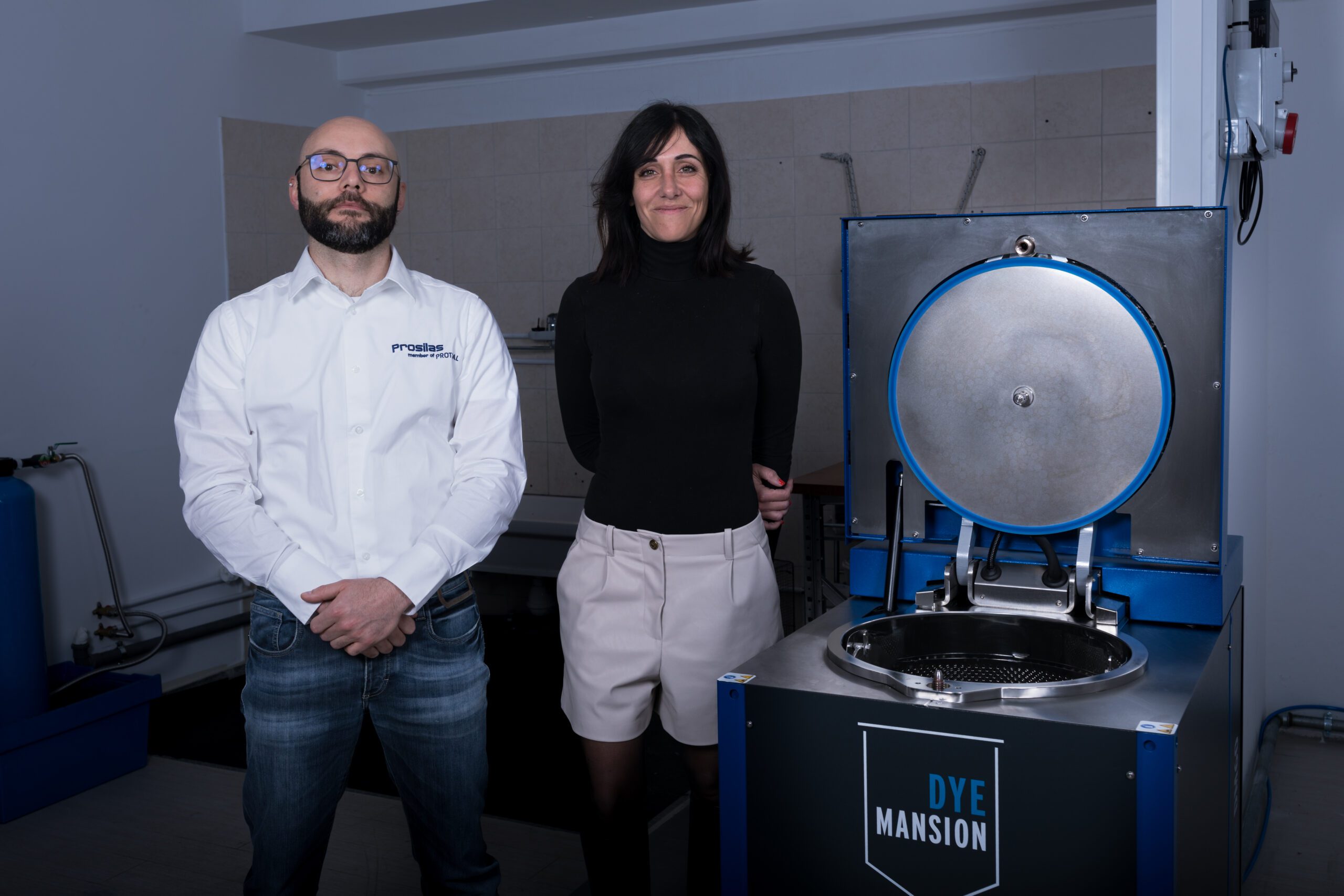
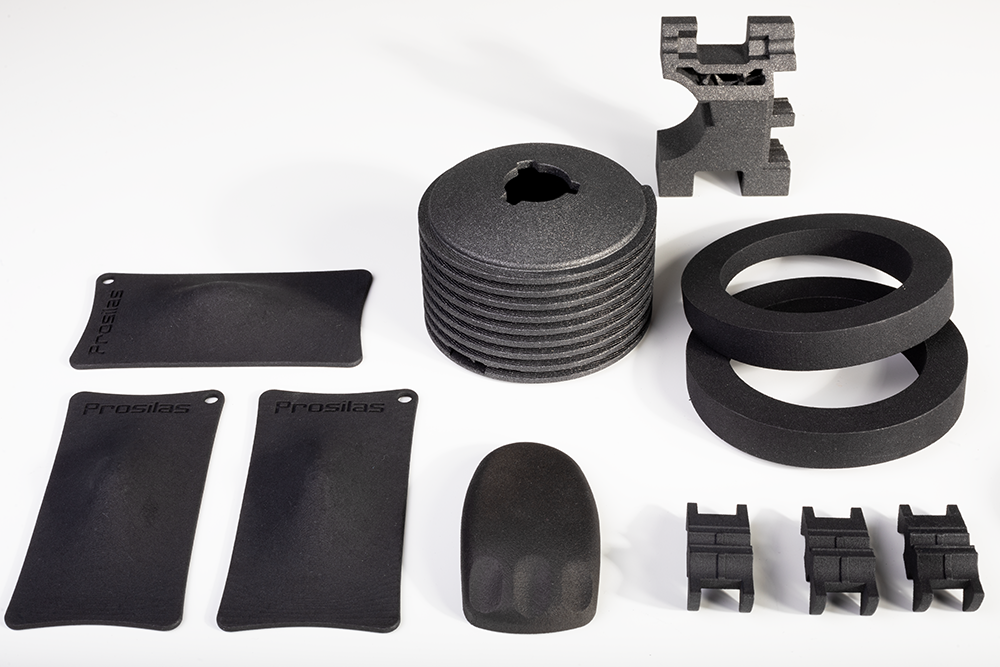
“We already had two other DyeMansion machines for finishing, the Powershot C and S models, so deciding to stick with this brand for automating coloring was the best choice,” says Vanna Menco, CEO of Prosilas. “Thanks to our collaboration with Energy Group (Digital Manufacturing Partner and a company within the SolidWorld Group), we identified and built the ideal package for our needs, and we are fully satisfied with it. Previously, coloring was done manually, which required time, attention, and constant operator presence. Now we can offer our customers a better and repeatable product even for industrial-scale production.”
The advantages of industrial coloring
The DyeMansion industrial coloring system is a great addition for Prosilas, as it offers advanced technology that allows for vibrant and long-lasting colors to be achieved quickly on a wide range of 3D printed materials: Pa2200, PA12 ALU, Pa12GF, Flame Retardant, and TPU. This results in parts that can be compared, even from an aesthetic standpoint, to those produced with injection molding.
This is a significant improvement in quality that enables us to meet demands for a variety of applications in the consumer goods, packaging, lifestyle, industrial, and automotive sectors.
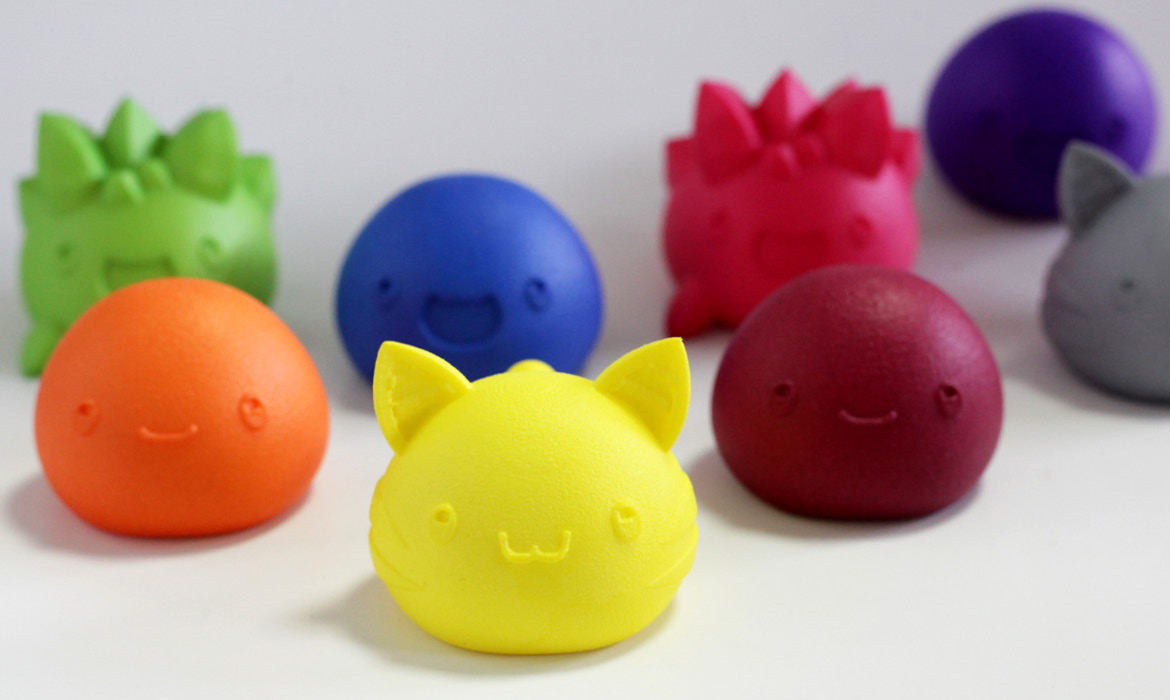
Our customers will be able to obtain 3D printed parts with excellent surface finishing, such as internal parts of cars, housings or parts of industrial machinery, objects for setups and customizations, and end-use objects with perfectly repeatable colors even for large runs.
“With a complete workflow using DyeMansion systems, we can now definitely satisfy more application areas. In particular, we can move from the world of prototypes and pre-series to that of industrial production, even regarding finishing,” concludes Vanna Menco. “We can now offer high aesthetic level 3D elements, satisfying sectors such as consumer goods, packaging, lifestyle, and automotive. Obtaining internal parts of cars, housings or parts of industrial machinery, objects for setups and customizations, and end-use objects with perfectly repeatable colors even for large runs is a significant improvement in quality for us and our offering.”
DyeMansion: a solution for our customers
A repeatable, automated, and reliable coloring process offers our customers a less expensive alternative to manual coloring. That’s why we have confirmed DyeMansion, a German company specialized in coloring and finishing of 3D printed parts, as an official supplier.
Their high-precision DM60 technology allows faithful color reproduction, offering a wide range of available shades.
Materials
PA2200, PA12 ALU, PA12GF, PA2210 FR e TPU.
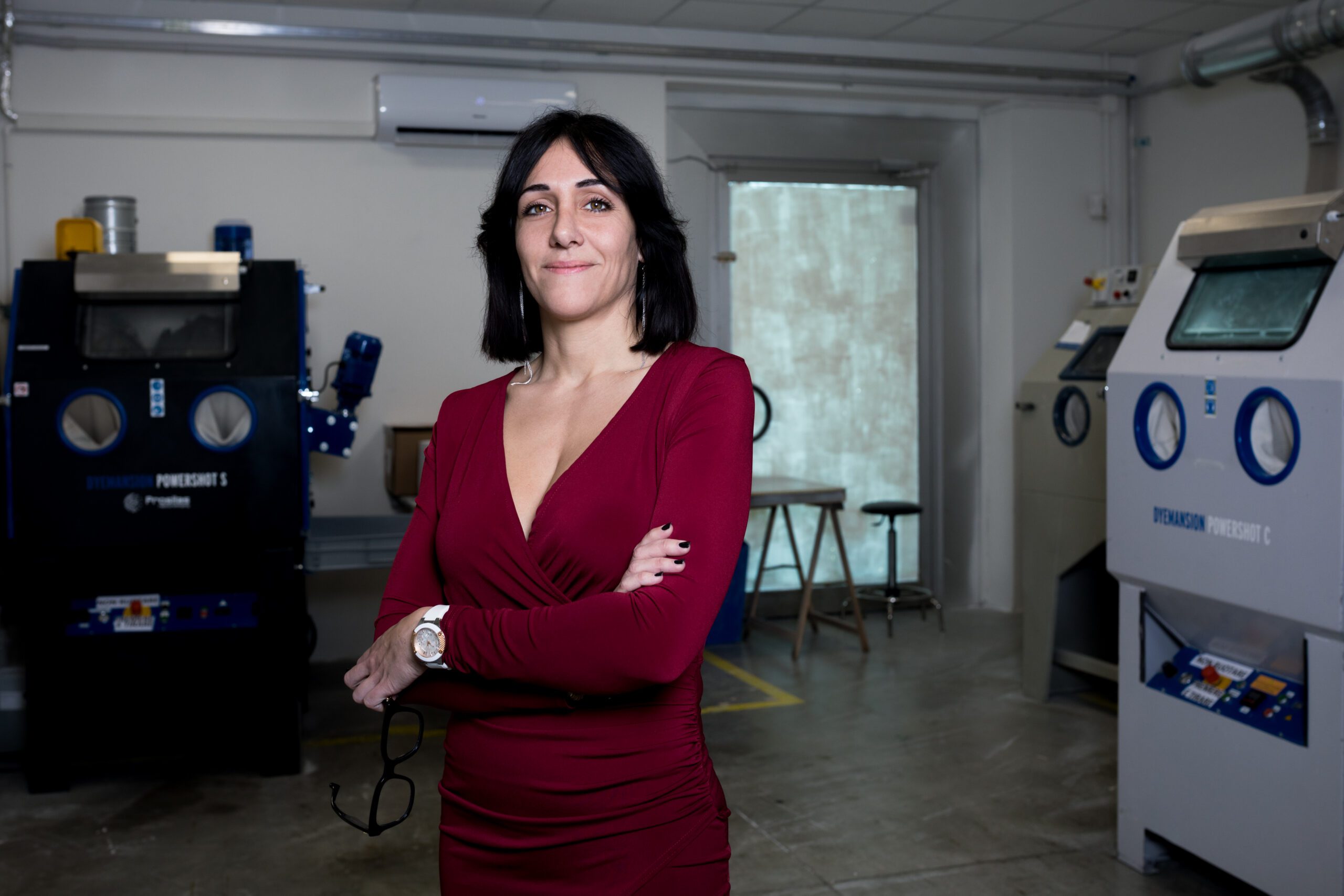
The acquisition of the Dyemansion machine demonstrates Prosilas’ commitment to providing companies with all the innovation through increasingly advanced systems.
The use of the latest technologies to improve production processes and ensure maximum satisfaction for an industry ready to grow.