Industrial Revolution: Performance and Design Optimization with SLS 3D Printing
3D printing as a viable alternative to CNC
Additive manufacturing and 3D printing technologies are emerging as effective alternatives to traditional CNC industrial systems.
In the following case study, we will explore how the use of our Selective Laser Sintering (SLS) 3D printing systems has allowed for the redesign and improvement of the performance of an industrial application.
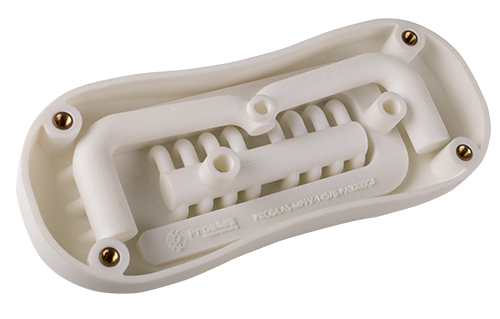
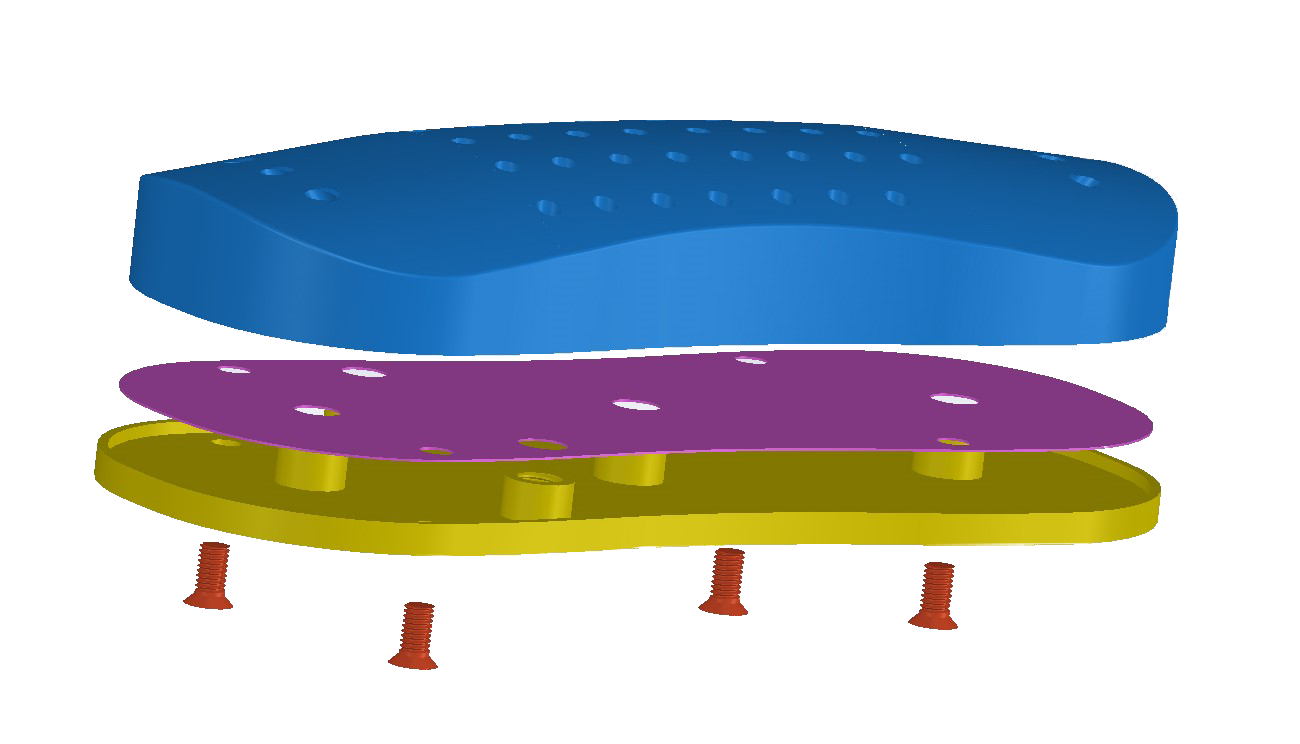
New Industrial Application:
The goal was to design a new gripping and handling component based on the principle of the suction pad with differentiated vacuum chambers, intended for the automatic machinery sector.
Project Objectives:
During the development process, we set several objectives, including improving the production performance of the automated line, reducing the weight of the component, addressing assembly challenges, and shortening the time to market.
- Improve the production performance (revolutions per minute) of the automated line on which the component is installed.
- Reduce the weight of the component.
- Address assembly challenges – monolithic part.
- Shorten the time to market.
Design for Additive Manufacturing:
We have embraced the principles of design for additive manufacturing and 3D printing, focusing on optimizing conventional geometry. This approach has allowed us to fully leverage the capabilities of 3D SLS systems, achieving innovative solutions that would be impossible with traditional techniques.
Throughout the redesign process of the application, we achieved significant results, including the optimization of integrated channel flows for air depression, weight reduction of the component while preserving its mechanical properties, elimination of two air depression grip points, and the integration of threaded metal inserts.
3D SLS Manufacturing Technologies and Materials:
The printing of the application was entrusted to Prosilas’ Selective Laser Sintering machines.
During the process, advanced materials such as polyamide PA2200 (biocompatible according to EN ISO 10993-1 and USP/level VI/121°C regulations, approved for food contact) and reinforced polyamides (e.g., alumide, PA12GF, PA2210 FR…) were employed.
It is possible to choose the optimal printing material for each specific need.
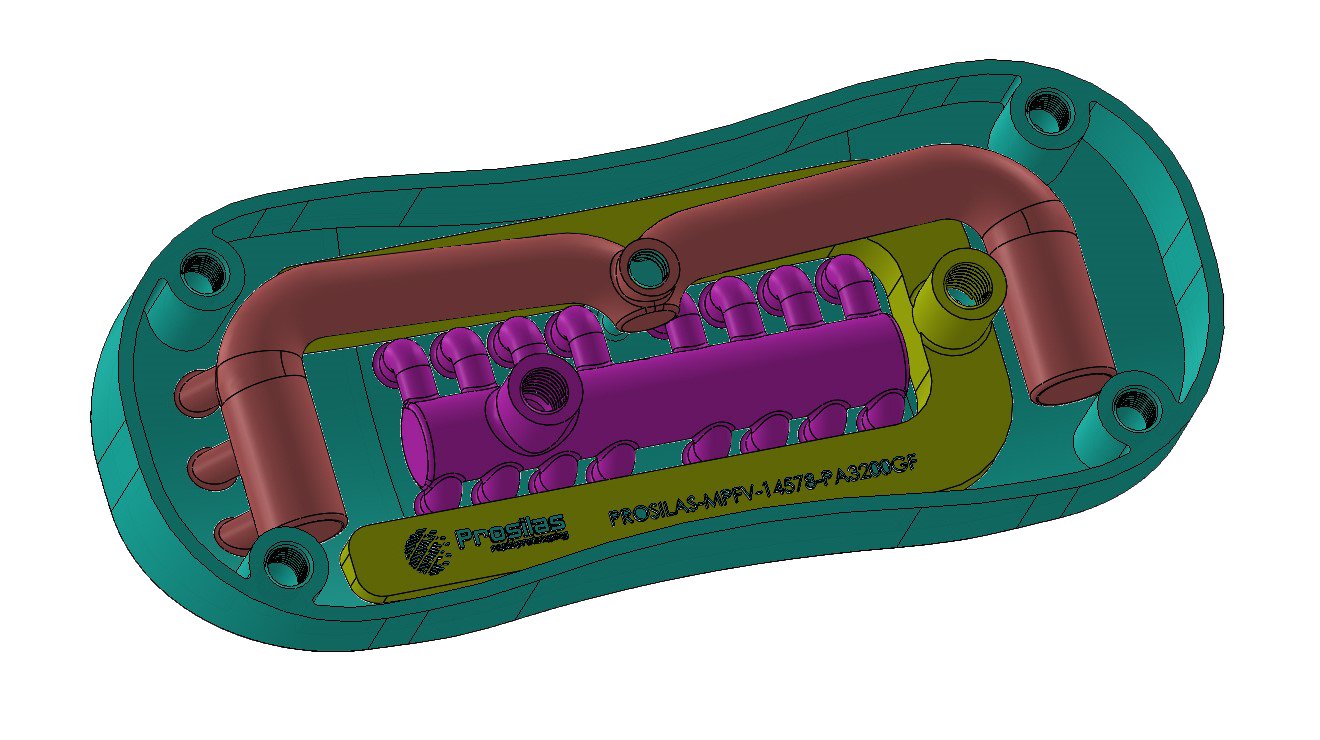
Advantages of SLS 3D Printing over CNC Systems:
1.Significant Weight Reduction of the Component:
Through a meticulous redesign and optimization process, SLS 3D printing has allowed for a drastic reduction in the weight of the component while maintaining structural integrity and required performance. This lightweight characteristic opens up new possibilities in terms of energy efficiency and dynamic performance.
2.Realization of Complex Geometries for Excellent Fluidodynamic Performance:
The design freedom offered by SLS 3D printing has enabled the realization of complex geometries optimized to enhance the fluidodynamic performance of the component. This ability to create intricate and functional shapes has revolutionized how we conceive and implement engineering solutions.
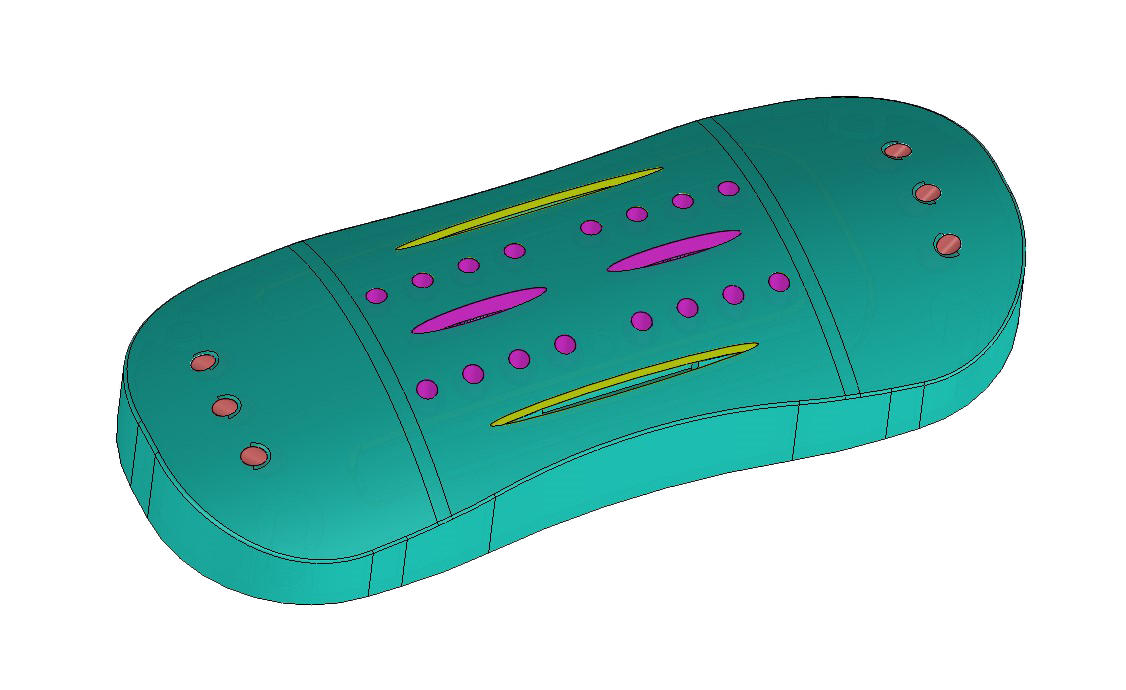
4. Part Consolidation for Simplified Management:
One distinctive feature of SLS 3D printing is the ability to consolidate multiple complex parts into a single monolithic structure. This not only reduces the total number of components in the system, simplifying assembly but also contributes to greater overall efficiency and durability.
5. Elimination of Seals and Simplification of the Connection Interface:
SLS 3D printing has allowed for the elimination of the need for complex seals, simplifying the component’s architecture and improving overall reliability. The machinery connection interface has been optimized, reducing grip points and enhancing overall integration into the automated line.
6. Overall Performance Enhancement and Delivery Time Improvement:
With the adoption of SLS 3D printing, there has been a significant improvement in the overall performance of the automated line.
Additionally, delivery times are considerably reduced compared to traditional machining, allowing for greater flexibility and responsiveness in the industrial context.
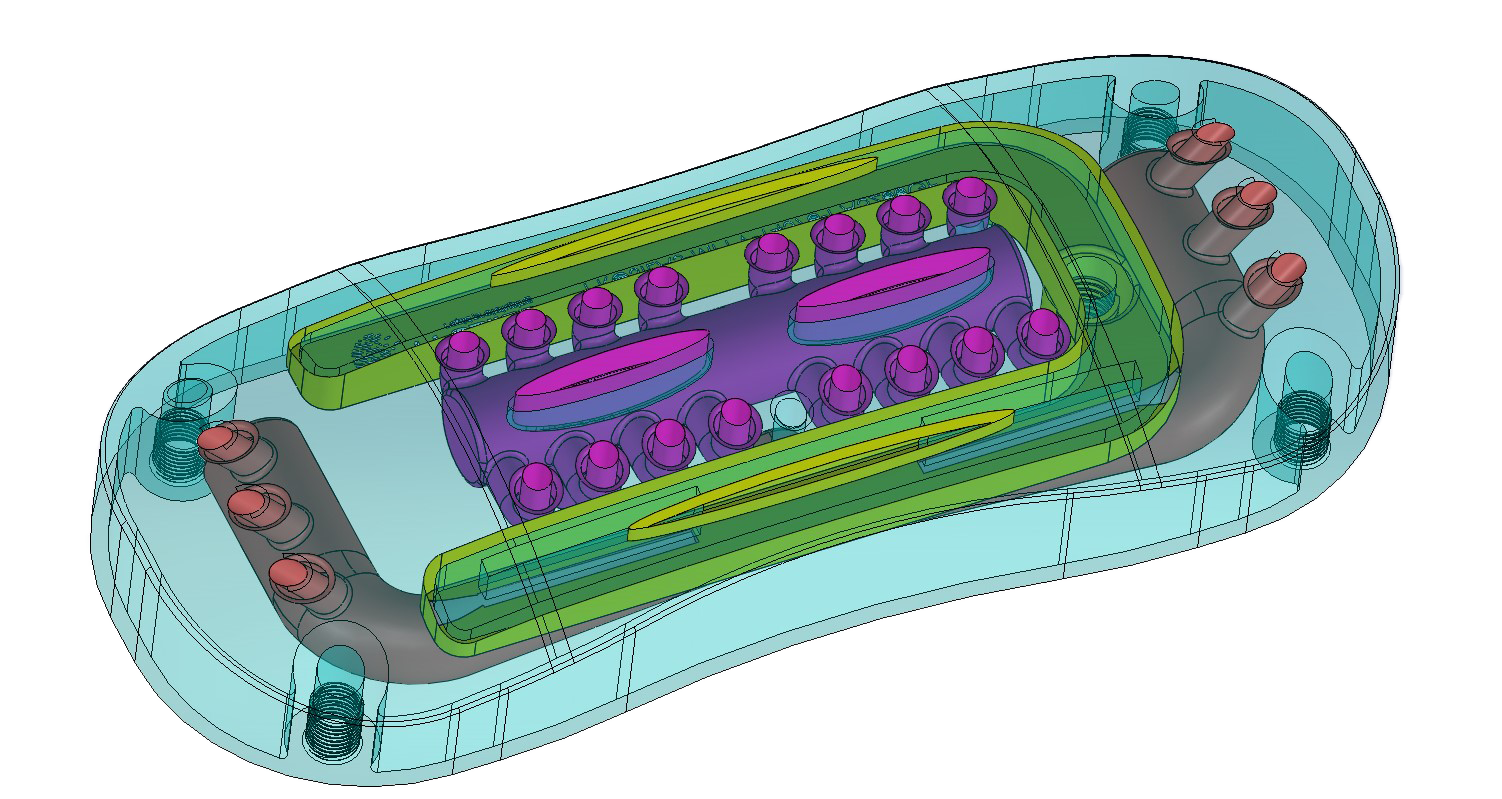
The evolution towards SLS 3D printing has proven to be a strategic choice, redefining the paradigms of engineering and industrial production through continuous innovation and unprecedented optimization.