Massimo Pierini Machine Operations Supervisor | Prototal Prosilas Voices of Prototal is our space...
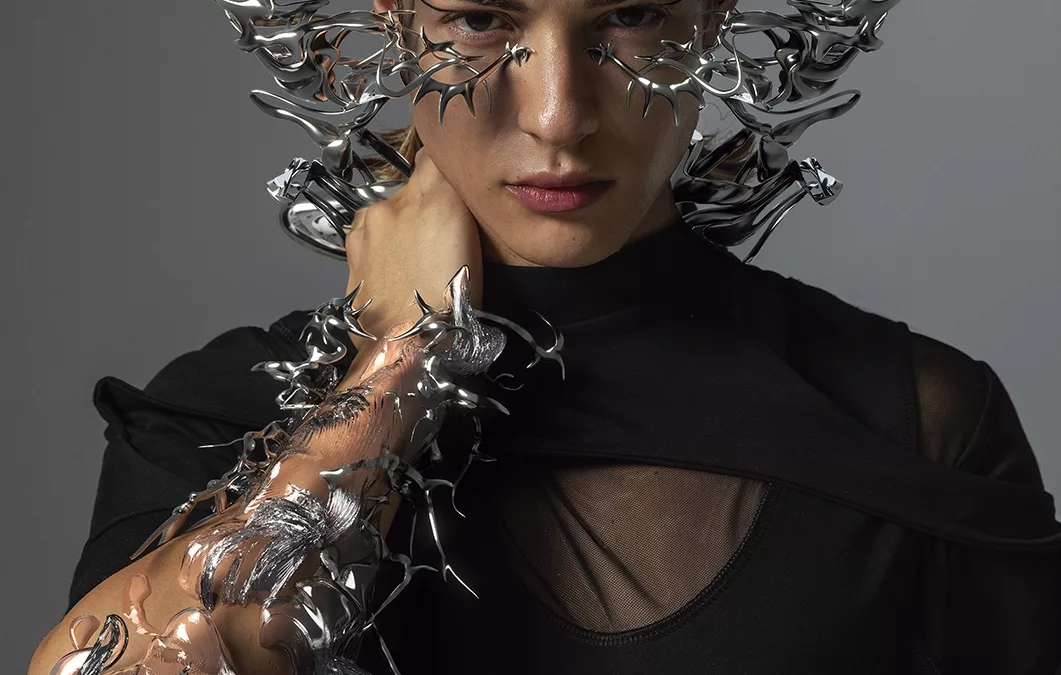
Made by Aliens
Case History
BASF Forward AM + JNORIG + Prosilas
“ I wish they looked like they were made by aliens” says Javier Giron, creative director of JNORIG.
Exploring Futurism and Sustainability in Fashion
In the heart of Barcelona, where diversity meets innovation, the avant-garde fashion brand JNORIG thrives.
Led by the visionary creative director, Javier Giron, JNORIG challenges conventions, embracing a futuristic aesthetic that celebrates individuality and self-expression.
In a quest to bring otherworldly designs to life, JNORIG embarked on a journey that led to an extraordinary collaboration with Prosilas and BASF Forward AM, resulting in the creation of truly remarkable pieces that seem “made by aliens.”
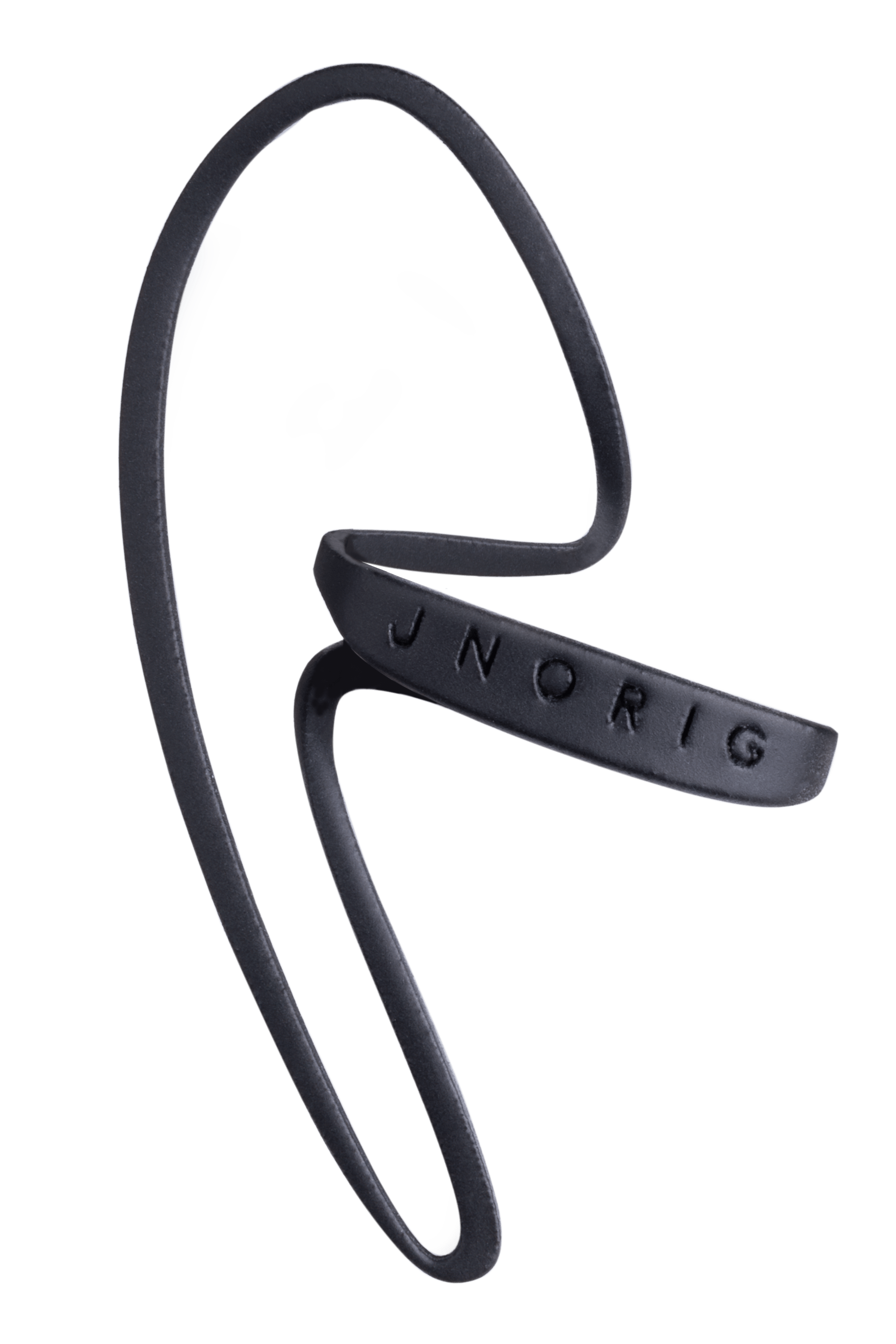
Challenge: Bridging Fashion, Sustainability, and Innovation
Fashion, by its very nature, is a realm of constant exploration and reinvention. It is a space where new ideas merge with cutting-edge technology and sustainable practices. It’s a shared DNA with the 3D printing industry.
When JNORIG expressed their desire for designs that defied convention and embodied sustainability, Prosilas and BASF eagerly accepted the challenge.
The task at hand was to produce jewelry pieces with unconventional shapes using sustainable materials, all while maintaining an impeccable level of surface finishing akin to creations from another world.
This challenge perfectly aligned with Prosilas and BASF’s commitment to pushing the boundaries of 3D printing technology and sustainable manufacturing.
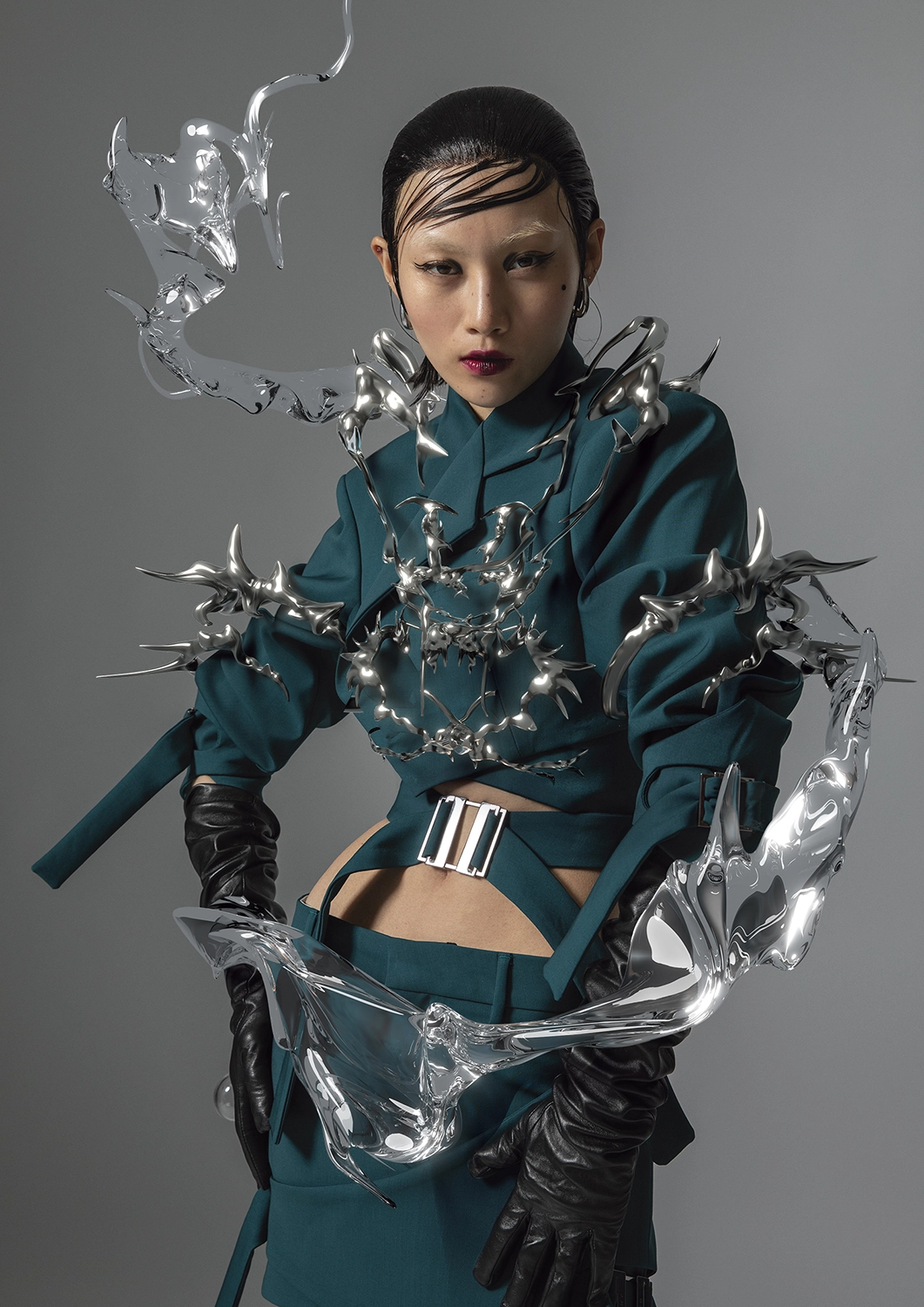
Solution: Ultrasint® PA11 – A Sustainable Innovation
Prosilas, in collaboration with BASF Forward AM, introduced Ultrasint® PA11 into their Selective Laser Sintering (SLS) systems.
Ultrasint ®PA11, made from castor oil, represents a bio-based alternative to traditional materials like PA12.
Its exceptional toughness, high elongation at break, and elasticity make it an ideal choice for creating resilient, impact-resistant parts.
Notably, Ultrasint® PA11’s biocompatibility and safety for human contact make it suitable for a wide range of applications, including medical devices and sensitive sectors.
Moreover, BASF’s commitment to sustainability extends beyond material innovation; they work closely with castor farming communities in India to enhance productivity and reduce environmental impact.
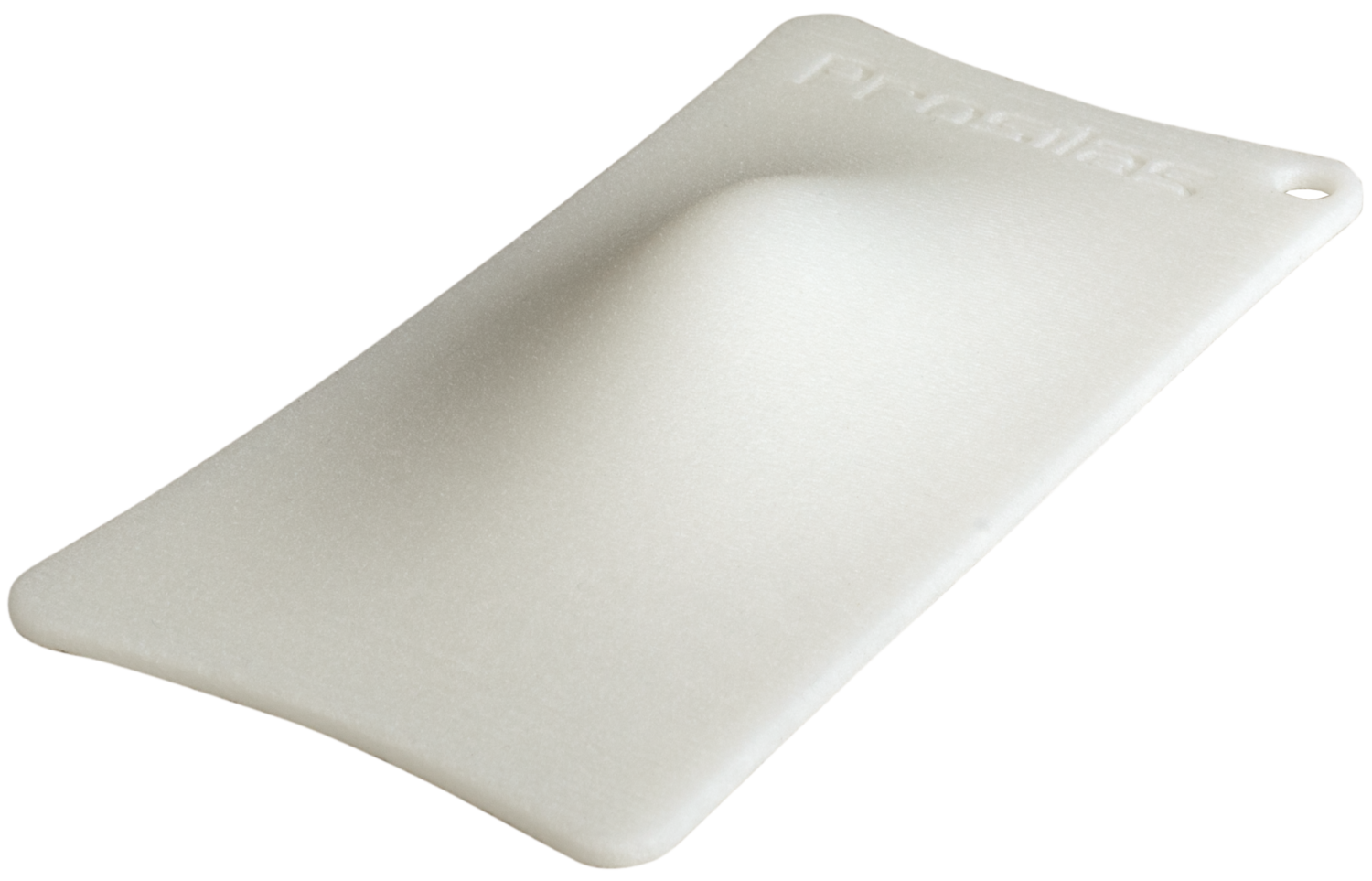
“Partnering with Prosilas on the ‘MADE BY ALIENS’ project highlighted our commitment to sustainability and innovation. Using our eco-friendly Ultrasint® PA11, they pushed the boundaries of 3D printing to bring JNORIG’s futuristic visions to life. This collaboration exemplifies the transformative power of combining cutting-edge technology with creative ambition, breaking the manufacturing boundaries in fashion, and beyond” says Marco Cristofori, Senior Product Marketing Manager, BASF Forward AM
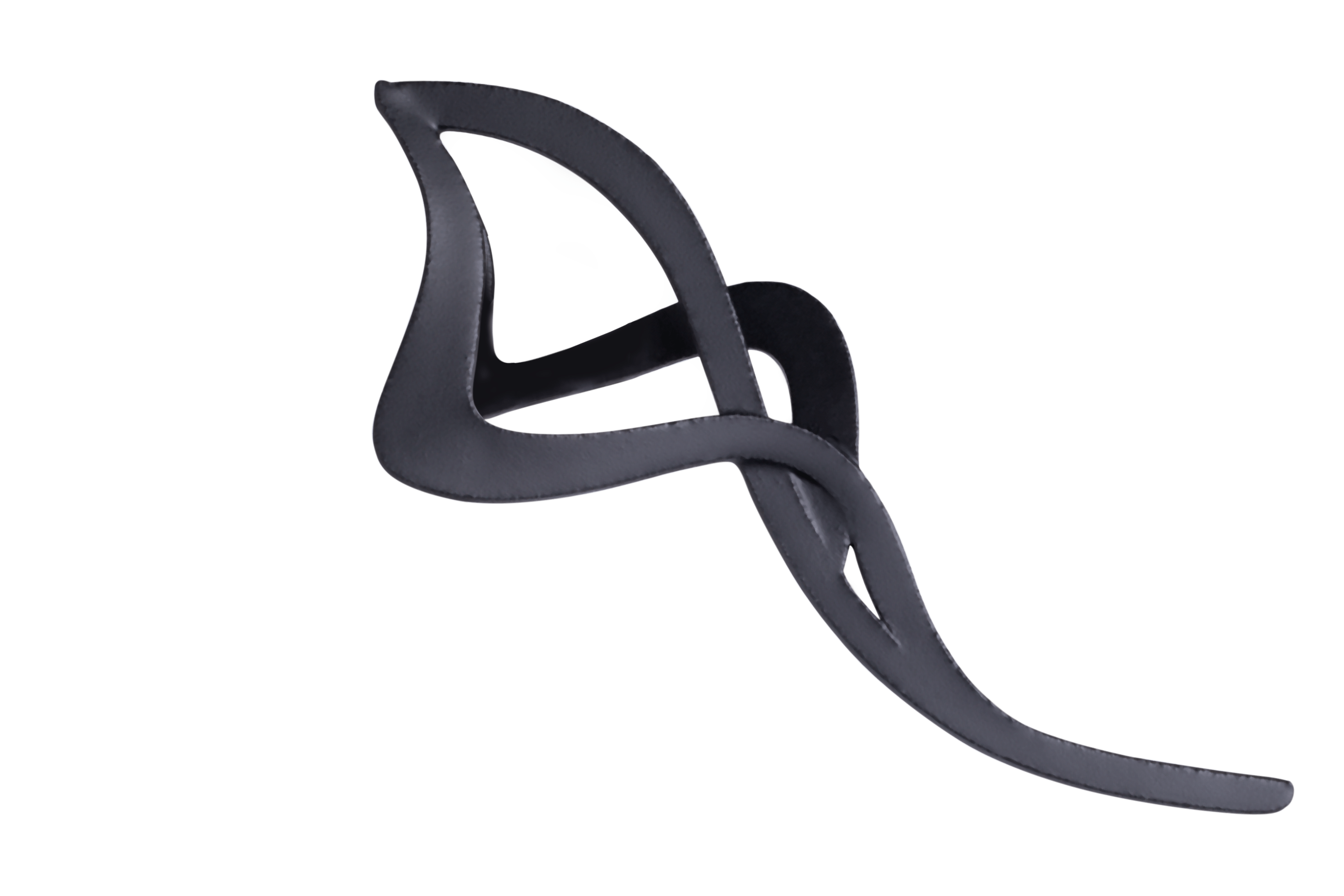
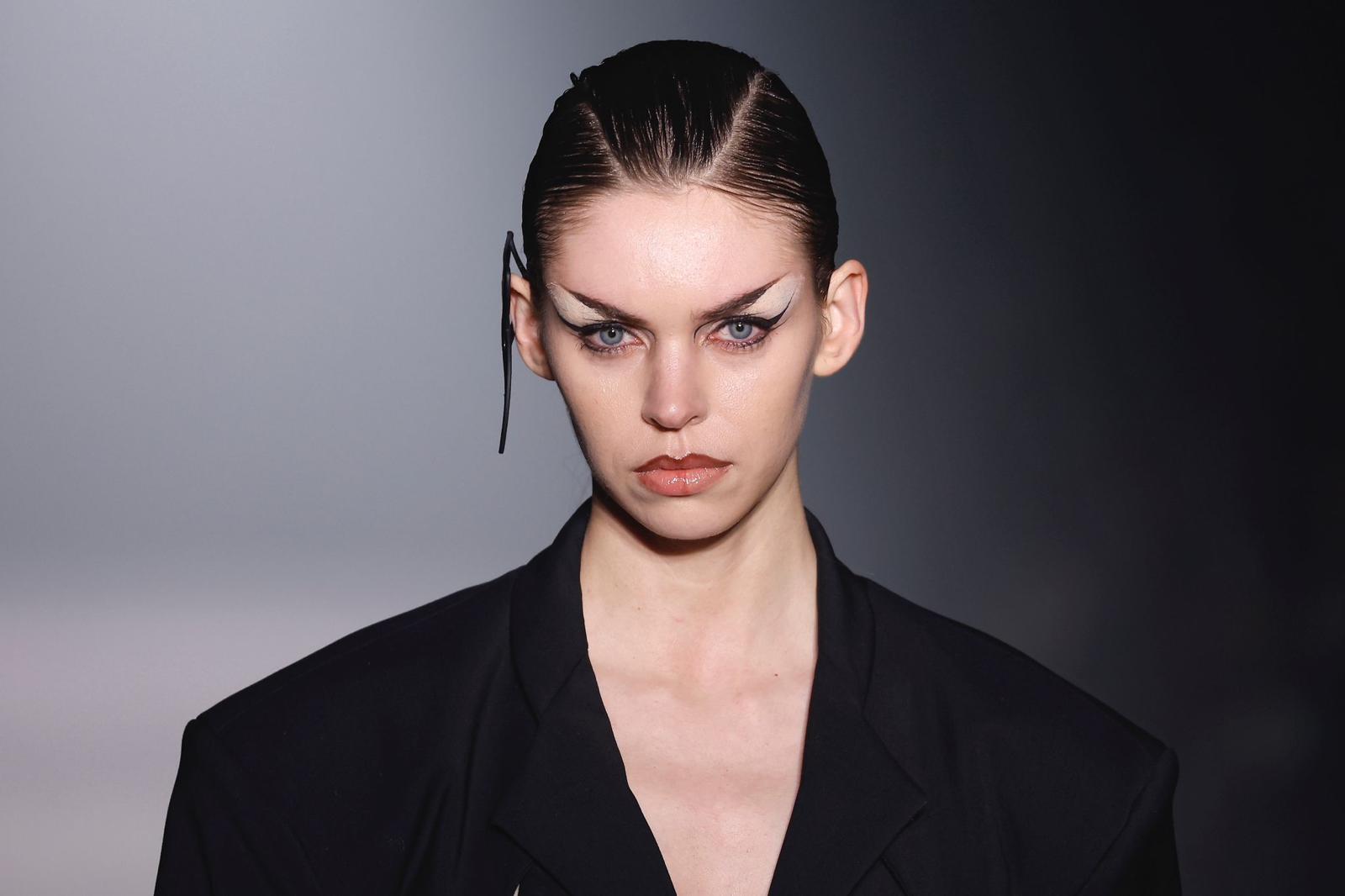
“In the world of fashion, innovation is the engine that drives designers’ creativity beyond limits with a distinguishing passion. For us, this market is a continuous source of inspiration and advancement in processes, constantly searching for new materials and finishes. Collaborating with JNORIG has been an incredibly stimulating experience: their innovative mindset seamlessly blends with the ever-changing demands of a market that evolves continuously, creating a bridge between the physical and digital worlds. It has been a privilege to be the connection between designers’ vision and product realization, transforming ideas into reality with enthusiasm and dedication,” shares Vanna Menco, CEO of Prosilass
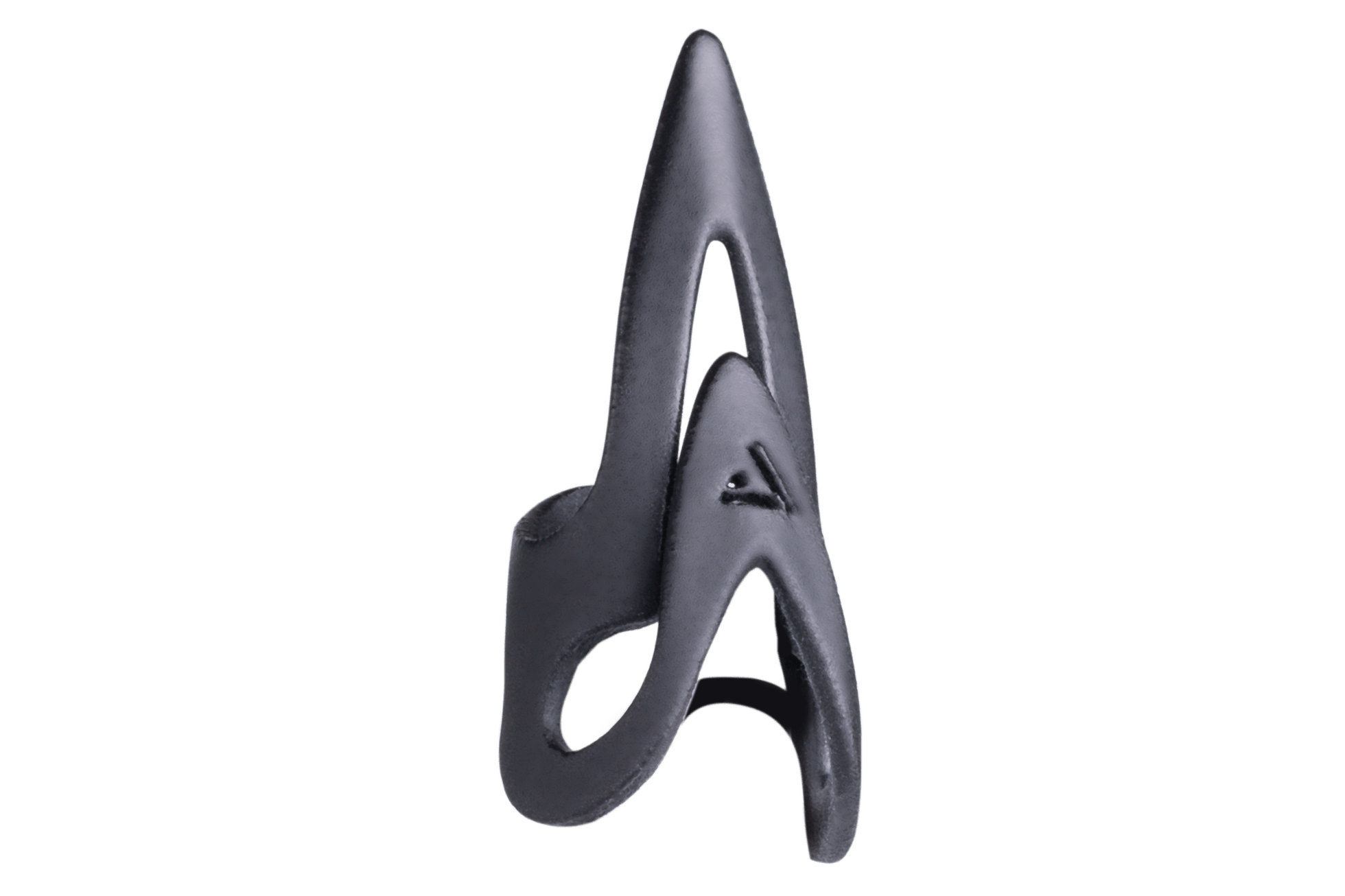
Collaboration Process: From Concept to Catwalk
The collaboration between Prosilas, BASF, and JNORIG was characterized by innovation, efficiency, and creativity.
Within just one month from the initial request, the teams transformed JNORIG’s visionary designs into tangible reality.
Using state-of-the-art 3D printing technology and advanced materials, they produced jewelry pieces that transcended conventional boundaries.
The designs, characterized by fluid silhouettes and otherworldly aesthetics, captured the essence of JNORIG’s futuristic vision.
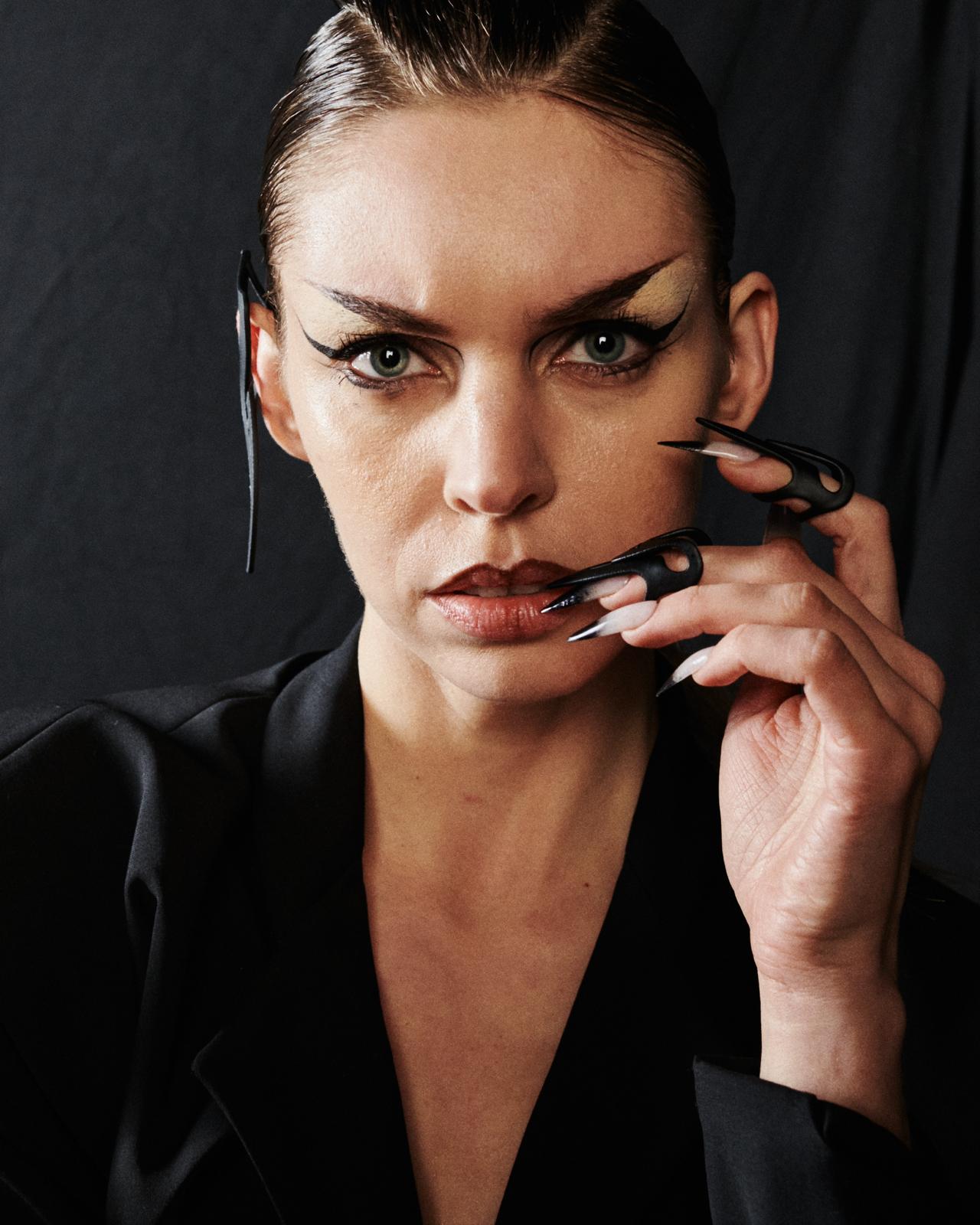
Fashioning a Sustainable Future
The culmination of this collaborative effort was showcased at the Barcelona fashion show on April 10th, 2024.
The jewelry pieces, crafted from Ultrasint® PA11, not only mesmerized the audience with their striking designs but also highlighted the potential of sustainable materials and advanced manufacturing techniques in the fashion industry.
JNORIG’s commitment to sustainability and innovation extends beyond individual creations; it represents a larger movement towards a more responsible and inclusive fashion ecosystem.
Through the fusion of creativity, technology, and sustainability, JNORIG, Prosilas, and BASF are pioneering a new era in fashion—one that is both visionary and conscientious.
In a world where the boundaries between imagination and reality blur, collaborations like these serve as a testament to the transformative power of creativity and innovation. As we venture further into the future, guided by the spirit of exploration and sustainability, the possibilities are as limitless as the cosmos themselves.
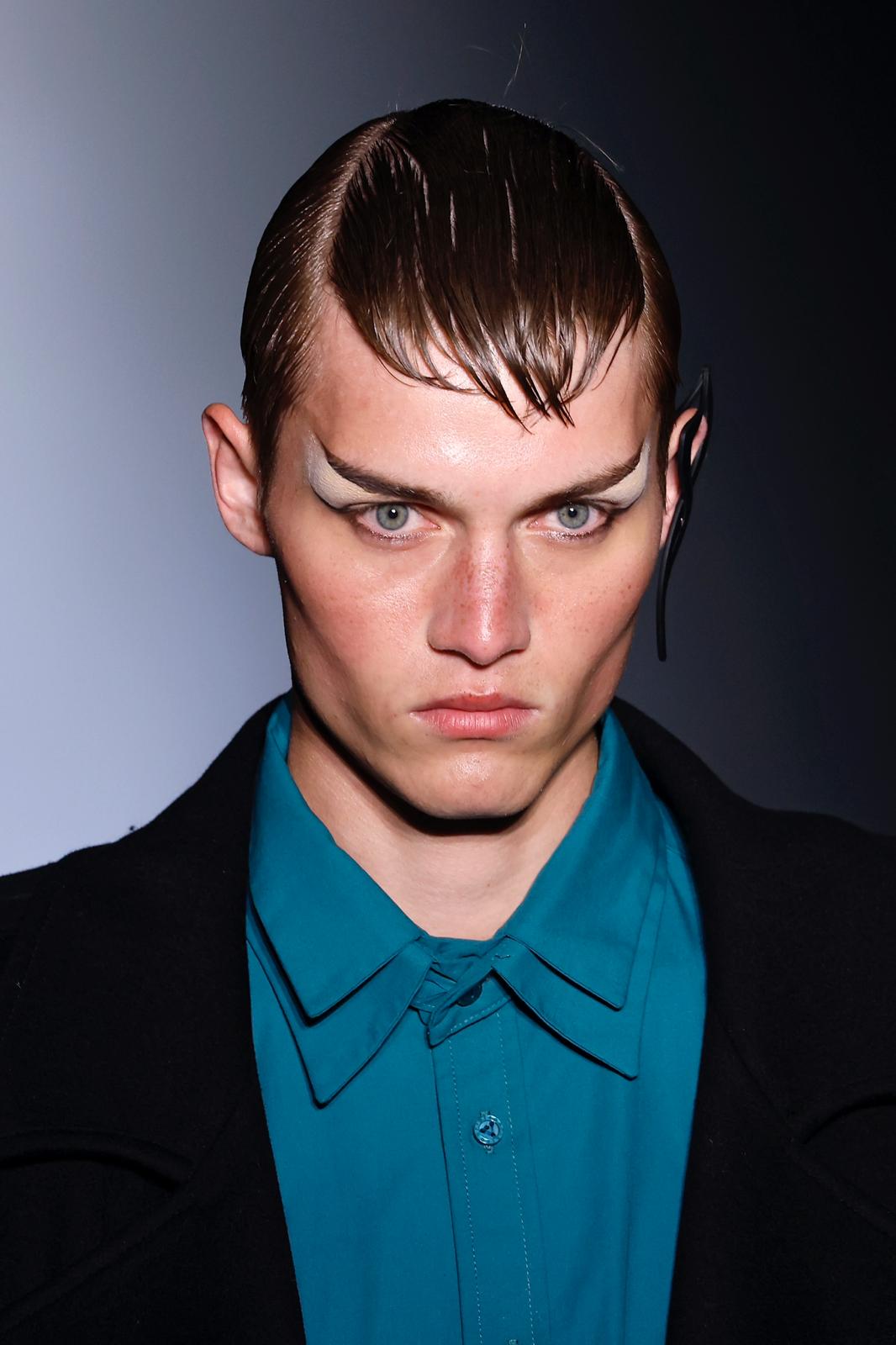
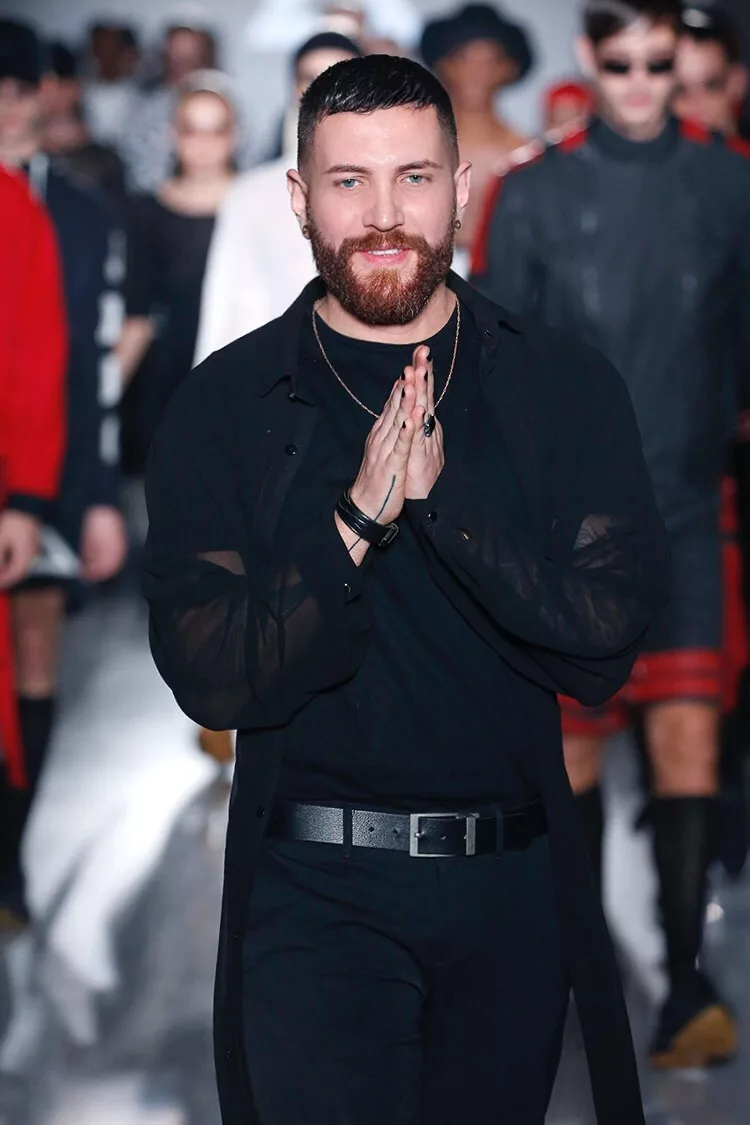
Javier Giron, designer JNORIG
FOCUS
JNORIG
JNORIG is a brand dedicated to diversity and breaking societal norms, celebrating individuality regardless of background, religion, or gender. With architecture-inspired designs and gender-fluid silhouettes, they blend cultural elements and opposing concepts for a unique artistic vision. Javier Giron’s innovative garments combine precision, comfort, and sustainability, embodying a futuristic aesthetic. Tailored for different body types, JNORIG’s designs promote confidence and self-expression, inviting wearers into a universe of disruption and mystique.
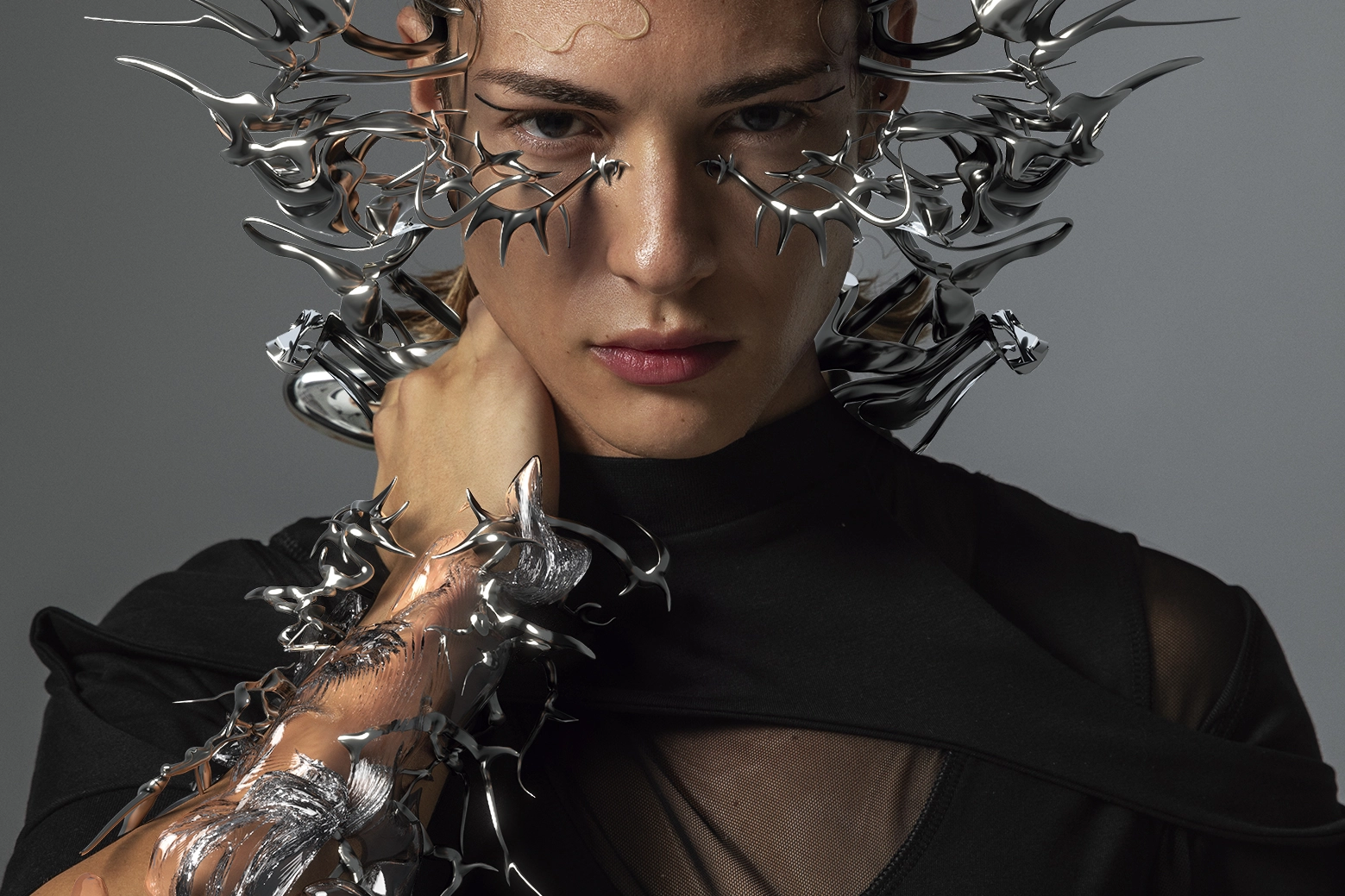
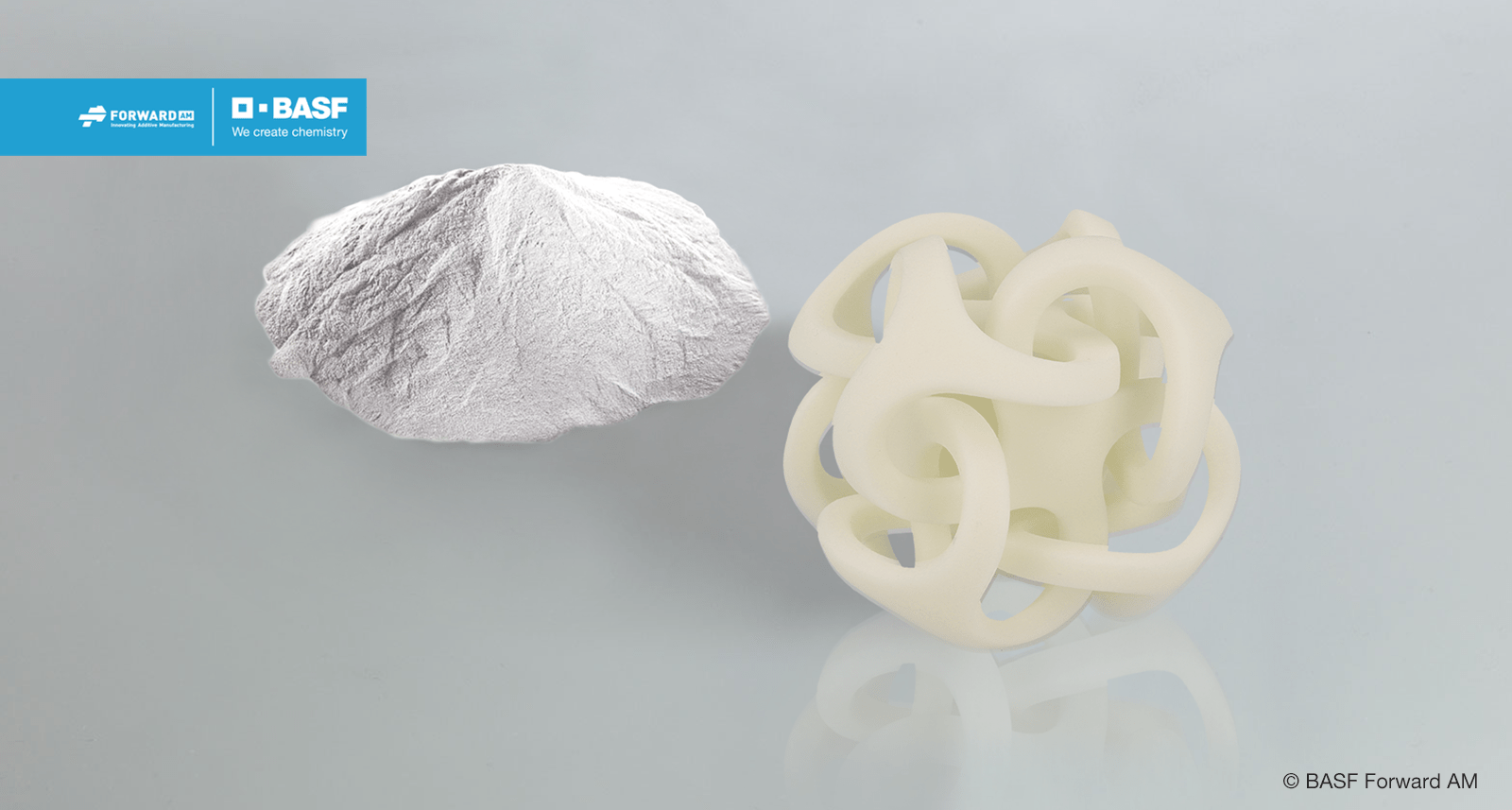
BASF Forward AM
BASF Forward AM provides 3D printing solutions along the entire Additive Manufacturing value chain: From consultancy and development, through bespoke design, digital simulation and prototype printing, to finishing and exhaustive component testing – Forward AM provides you with exactly what your business needs. Whichever material you require for your specific project, Forward AM offers you the world’s largest selection of 3D printing materials and service solutions.
Prosilas
Established in 2003 and part of the Prototal Group since 2022, Prosilas stands out as an advanced service provider that integrates various technologies, from 3D printing to vacuum casting and injection molding.
With a strong customer focus and proven experience, Prosilas is a reliable, fast, and sustainable partner for the industry. The company is a reference point for series production, with a long-term vision and the commitment to completing the production cycle by satisfying every phase.
Prosilas offers its expertise in industrial processes and polymer materials to meet the new market demands. Prosilas promotes the research of innovation on products and solutions, with the aim of reducing waste and intensifying research in an efficient and sustainable way.
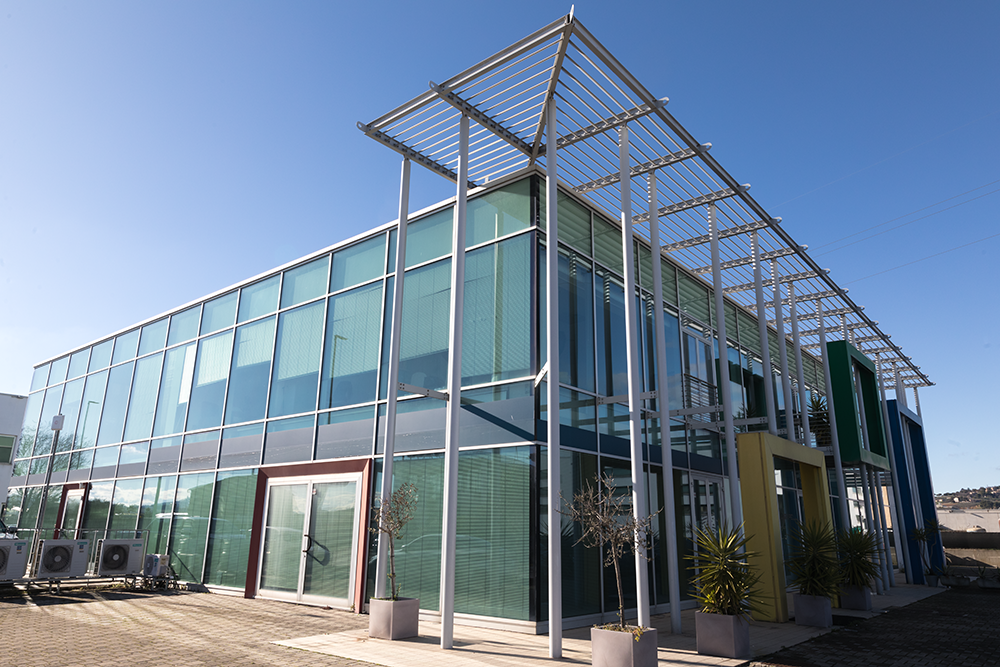
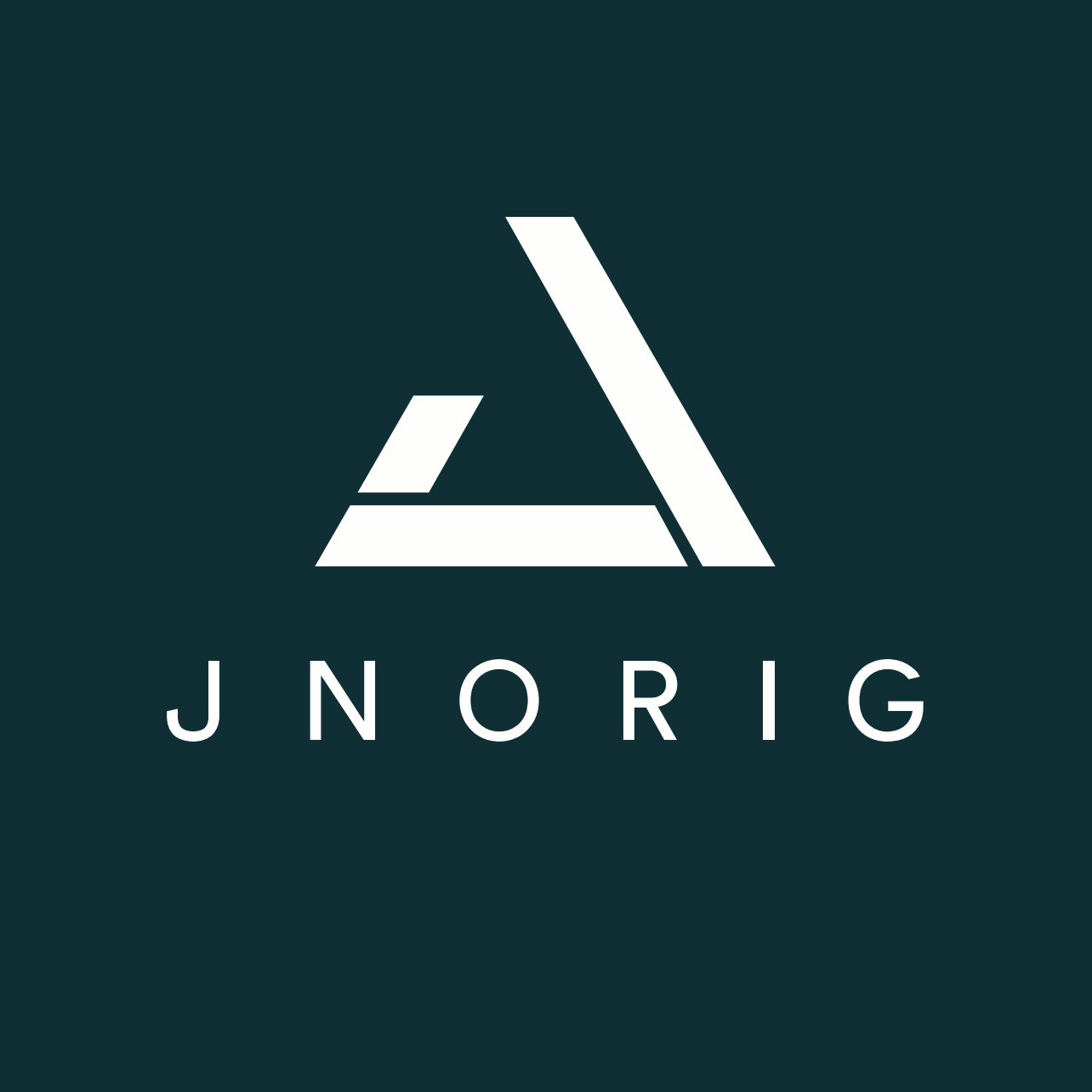
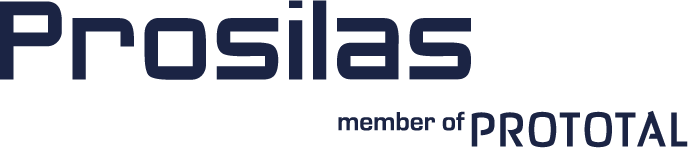
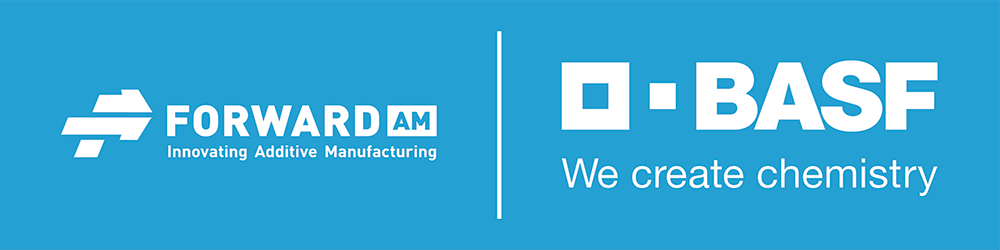