Thanks to the constant evolution of 3D printing we can measure ourselves with new challenges to meet industry needs daily.
Dynamic workflow
3D printing evolves and progressively improves its performance, allowing us to measure ourselves as production supplier even on a large scale, through a set of procedures modulated on each individual customer that become a fluid progress towards the winning solution.
Today we discuss the topic of additive manufacturing on an industrial scale together with Vanna Menco (CEO Prosilas) and our technician Roberto Nasini.
We assume that additive manufacturing was born for rapid prototyping, as the fastest and most optimized system to develop prototypes.
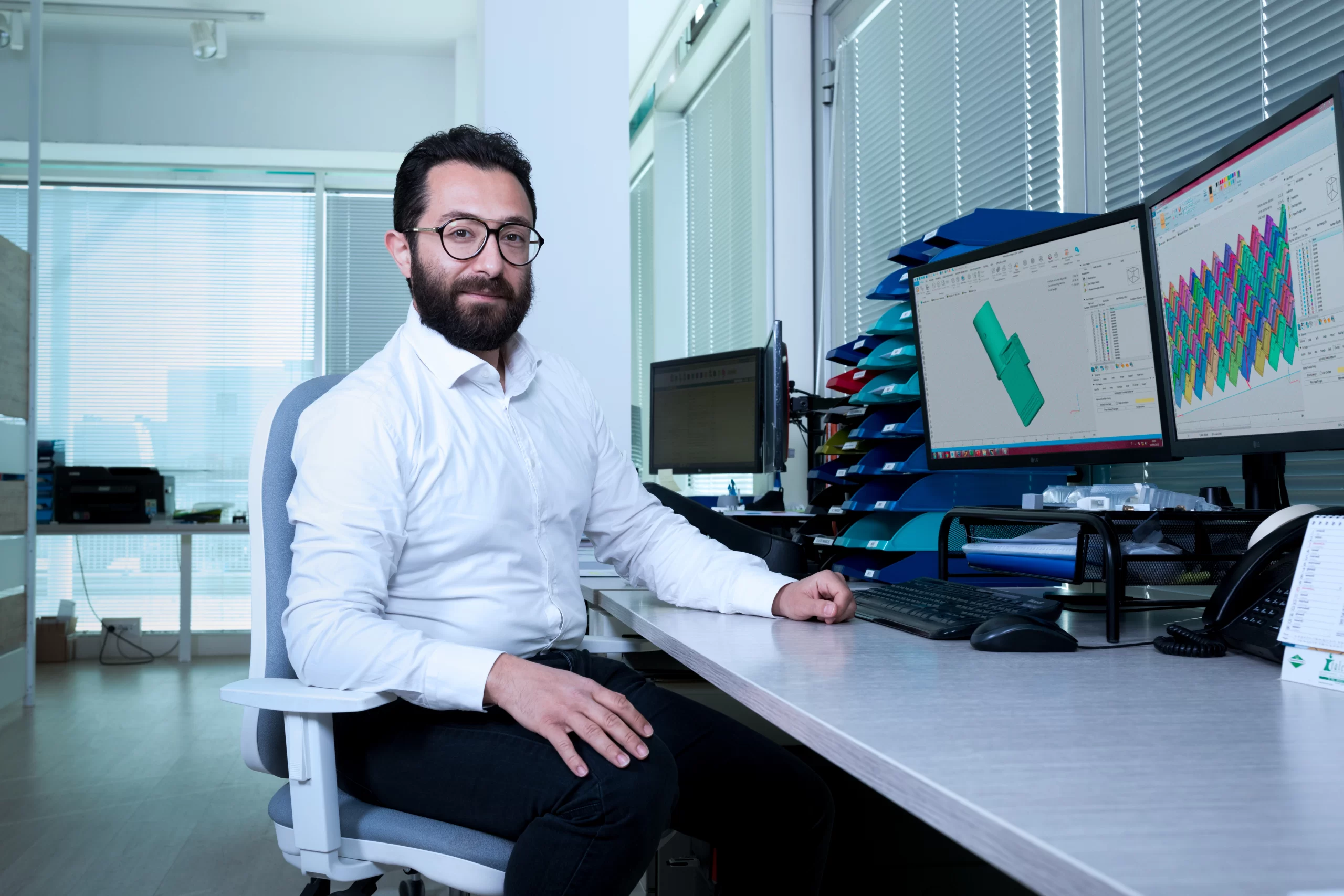
However, it can happen that technology goes beyond its borders, as in this case, progressively conquering ground to reach production volumes that go far beyond the few pieces.
In the case of industrial scale production, in fact, AM can become a fundamental part in the process of Life Cycle Assessment of the product, within stages that adapt from time to time to the new realization.
The importance of design for additive and optimization in large-scale production
“Our customers have very different production needs. The objects that we are required to make, especially the first time, have often been designed for other technologies, such as injection molding. In this case we can ask to adapt the model to be printable with the technology, mainly SLS, intervening on thickness and dimensions”.
This co-design phase is often necessary to study and understand where the object can be improved, for example, with geometry optimization or with mechanical reinforcement. Sometimes you look for a different performance, other times the need is to get the same performance but with different materials.
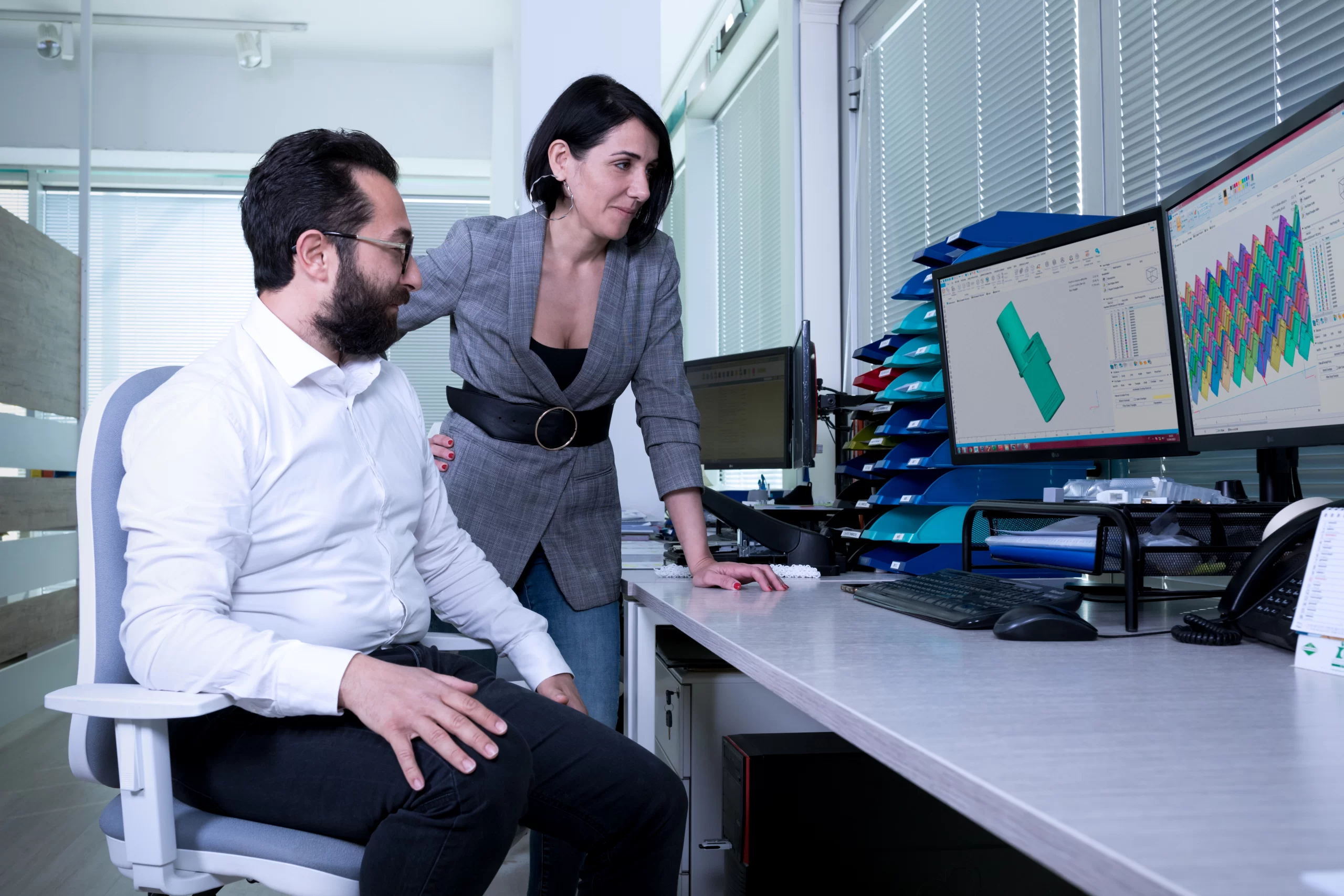
“You can make more or less substantial changes in mathematics, reasoning on an industrial scale, to optimize consumption, aesthetics and performance by eliminating for example material where it is not needed and creating structures (as in the Voronoi model) that lower production times”.
Always thinking in the perspective of a large-scale production, it can also be useful to consider a complete re-design (or design) of the piece, with functional or aesthetic purposes: think for example to the design of a lighter sole than the original model, for which a series of adaptations are proposed to create a design with the same shape but printable in 3D with a solution of latex structure, more practical than other materials or more traditional methods.
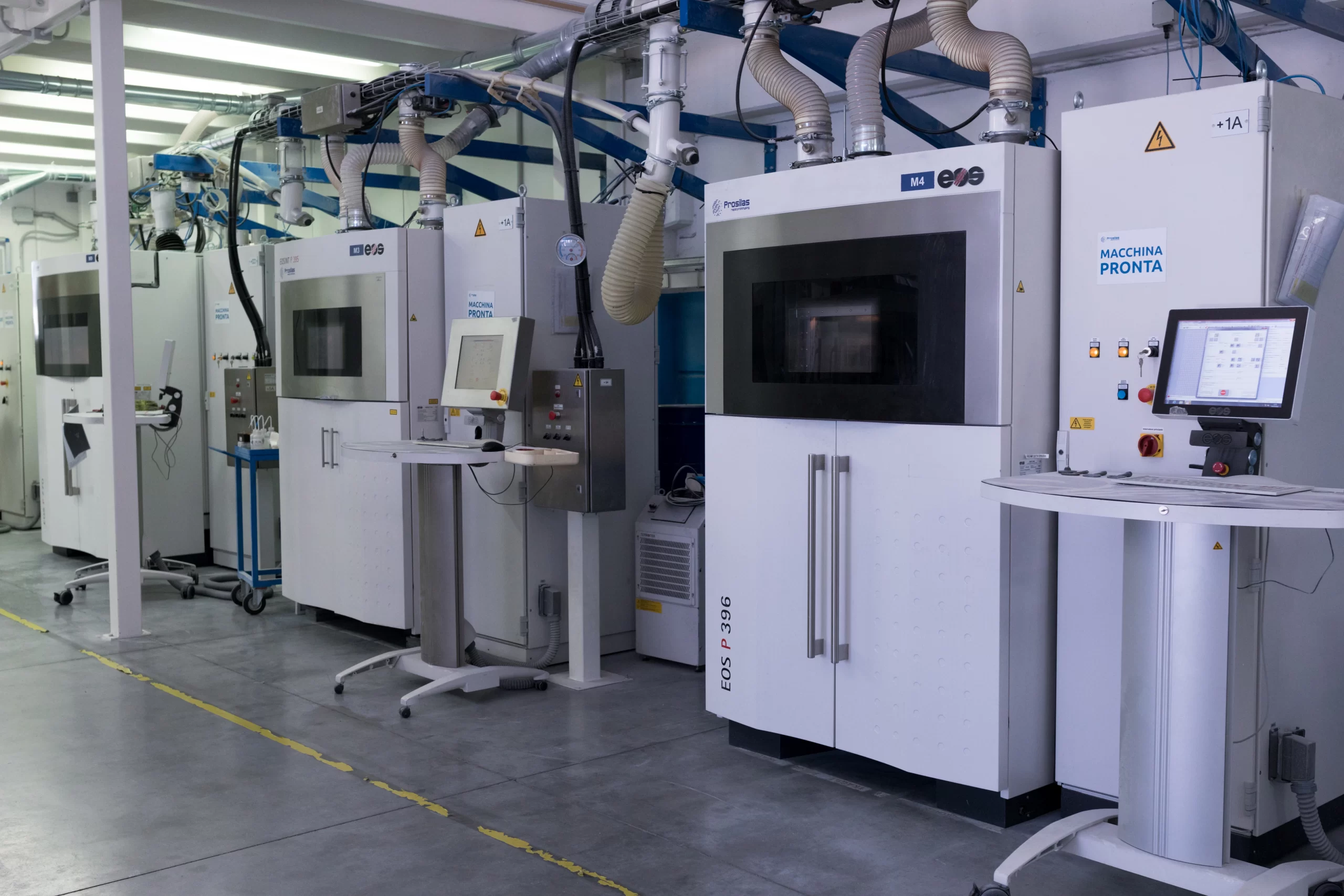

The goal? Reducing production time
In both cases, co-design or re-design, there is a work with the customer, with approval of each proposal by the technical department. The basic objective, thinking of a production on industrial volumes, is often the lightening of weights: not so much to reduce the costs related to the use of material, but rather to use less time in theprinter. The right balance between material reduction and machine time.
This is the key role that gives the possibility to increase productivity. To make the most of this element, we propose structures suitable for mechanical performance, which are easier during printing, according to the timing of a production cycle already tested. All this so that the customer has the highest productivity in the shortest time, otherwise the cost will not be competitive.
The right steps for more efficient additive manufacturing
Producing on a large scale, especially with SLS technology, it is also crucial to understand the better machine orientation of the part. “Together with the customer we wonder what is the purpose of the object – mainly aesthetic or mechanical – and working conditions”. The answers affect the orientation and optimization of the various parts in the machine, always to achieve a saving of time and greater productivity by making several parts together.
This is coupled with a study of production cycles that ensures maximum productivity: for example, that machine changes are continuous, locking the print queue for more efficient production and programming the machine change during working hours.
The choice of material also plays a key role: it takes place during the co-design phase and undergoes an important verification during pre-production with test pieces (pre-series), to evaluate the product before launching into large productions. “The most typical case is when the customer tells how ‘he has always done’ and what he uses with other technologies. Here the advice and the address intervene, depending on the result you want to obtain”.
The role of 3D printing for large-scale production is therefore growing. But what is missing to get to make the most of this system?
The aspects on which it is necessary to intervene are the speed of the machines and the automations, that is the processes that do not depend on the presence of the personnel. In both SLS and SLA 3D printing you study in that direction. The future, however, really seems to be coming. Already in 2020 a company like Prosilas saw in its work 70% of prototypes and 30% of production. Today the trend remains growing and technology will soon be ready for the next jump.
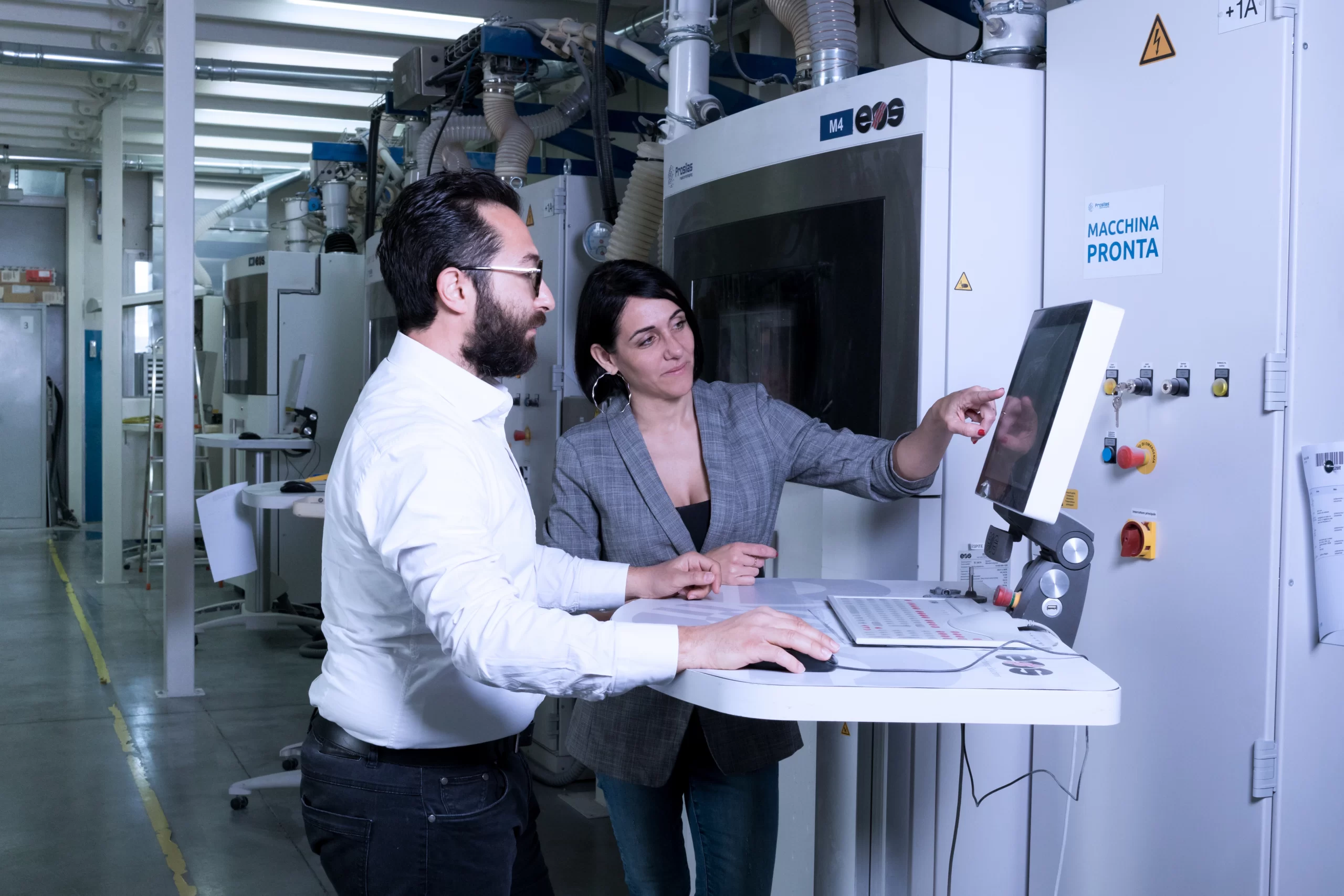

ROBERTO NASINI
Senior Technician
Roberto Nasini is member of the TAB – Technical Advisory Board of the Prototal team, as well as being one of our most experienced technicians, both for the use of SLS technologies and for SLA, responsible for feasibility assessments, use of 3D scanning and reporting systems, estimation and technical support.