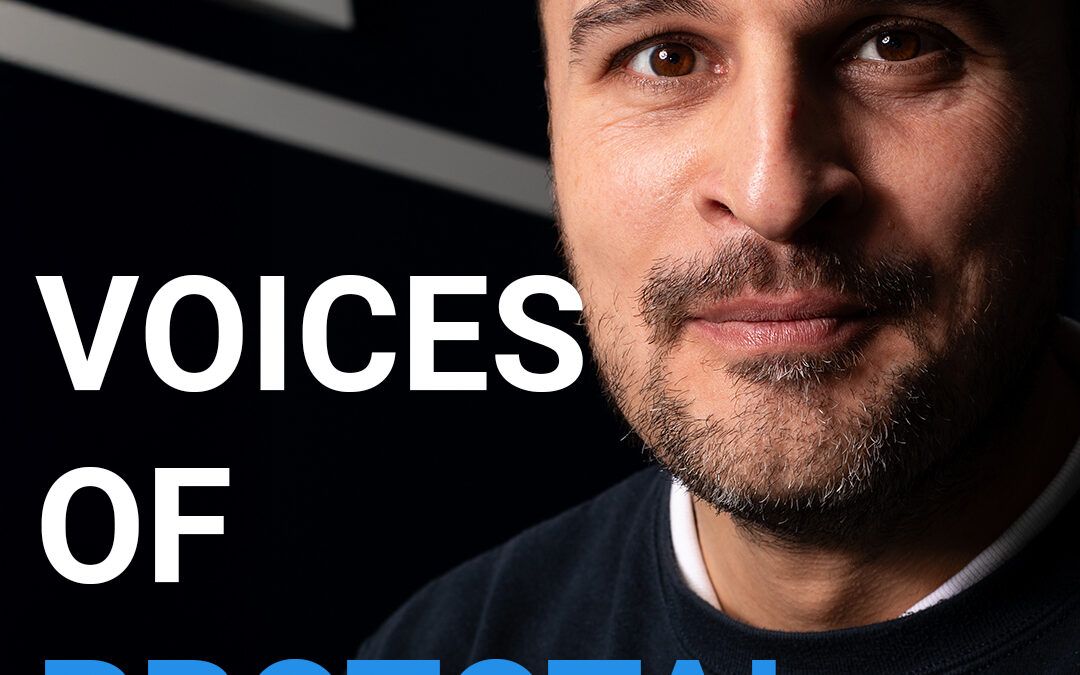
Voices of Prototal – Luca Ferroni
LUCA FERRONI
TECHNICAL MANAGER
“Un compito fatto con superficialità non porta soddisfazione. E spesso richiede lo stesso tempo che serve per farlo bene.”
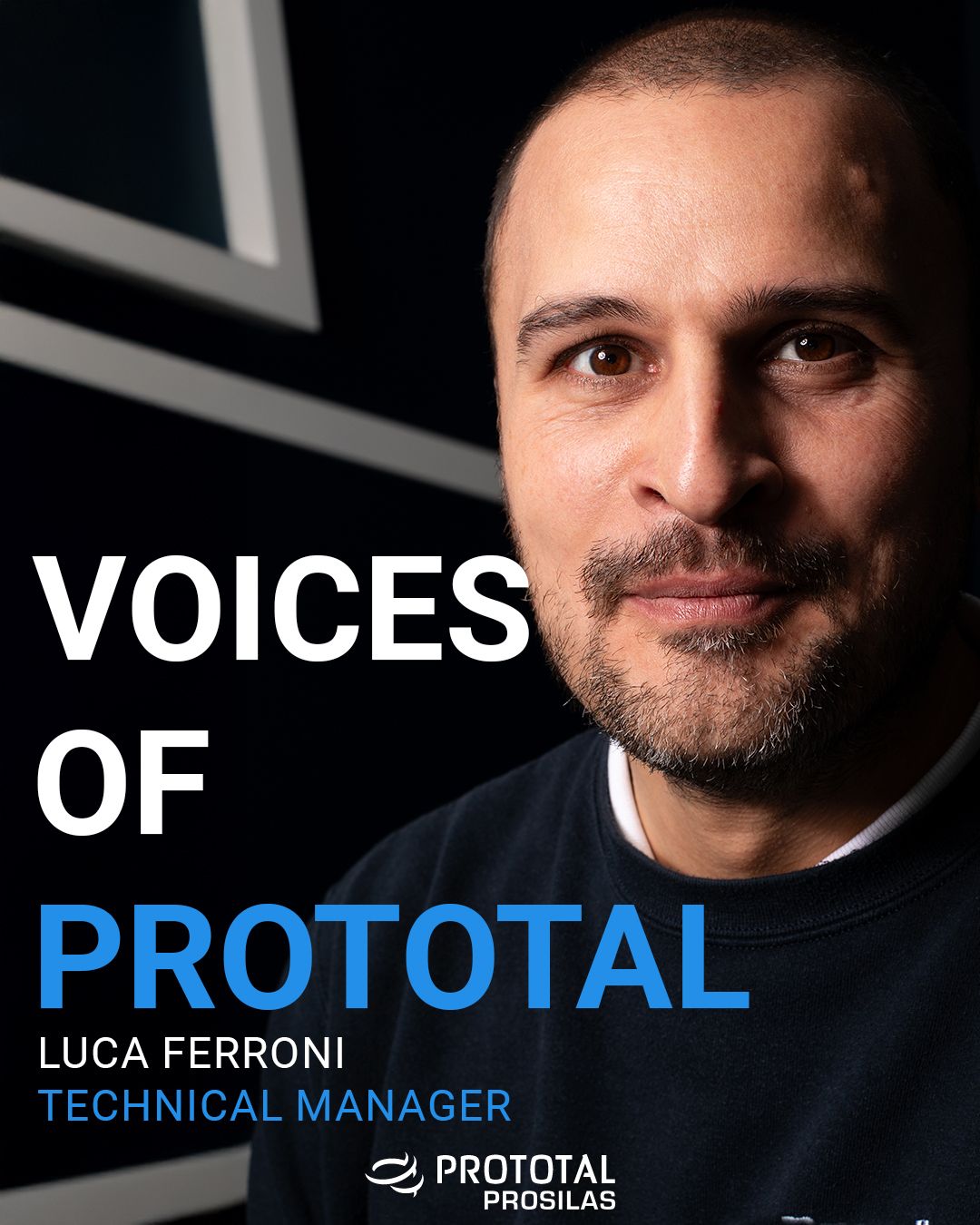
Qual è il tuo background professionale?
“La mia passione per il 3D è nata quasi per caso, ma ha cambiato tutto. A 19 anni, ho seguito un corso di grafica computerizzata e progettazione per prototipi per il mondo della calzatura. Non immaginavo dove mi avrebbe portato, ma è stato lì che un docente mi ha suggerito di provare a entrare in Prosilas. Nel 2003 ho iniziato il mio percorso come primo dipendente dell’azienda. Da allora sono passati 20 anni, e ogni giorno continuo a scoprire quanto questo lavoro possa essere affascinante.”
Cosa ti dà energia fuori dall’ufficio?
“Fuori dall’ufficio cerco di bilanciare le cose. Passo più tempo possibile con mia moglie, mia figlia di 9 anni e il nostro cane. Amo la fotografia, e condividere questa passione con mia figlia, magari durante una passeggiata in montagna, è una delle cose che mi dà più energia.”
Come ti mantieni motivato e qual è la tua filosofia di lavoro generale?
“Per me lavorare bene è una questione di passione. Ci vuole impegno per ottenere grandi risultati, e sono convinto che le sfide – quelle vere – siano le occasioni migliori per crescere. Mi piace trasmettere entusiasmo e motivare chi lavora con me, anche se non sempre è facile. Però quando il team rema nella stessa direzione, accadono cose incredibili.”
Orgoglio e difficoltà
“In questi anni, mi sono trovato spesso davanti a sfide che sembravano impossibili: processi considerati irrealizzabili, materiali difficili da lavorare, produzioni estremamente complesse. Eppure, ogni volta ci siamo riusciti. Dalle parti in caricato carbonio agli stent tracheali in PCL, ognuno di questi risultati è stato una conferma di cosa possiamo fare insieme. Ovviamente, ci sono stati anche momenti difficili, come durante il COVID. Ma in situazioni come quelle, la fiducia nelle scelte e la collaborazione del team fanno davvero la differenza.”
“Sono curioso per natura, e questo lavoro mi tiene sempre sulle spine. Il mio obiettivo è continuare a migliorarmi, affrontare nuove sfide e dare il massimo per Prototal. Le responsabilità non mi spaventano, anzi, mi motivano.”
“Il mio consiglio per chi inizia? Non lasciare spazio alla superficialità. Studiare e approfondire sono la chiave per crescere, in questo settore come in ogni altro.”
Luca Ferroni – Technical Manager Prototal Prosilas